What is DTG Digital Printing (Direct-To-Garment)?
There are many printing methods available on the market for you to choose from, but the most popular is direct-to-garment printing (or DTG printing). Choosing the right printing method will determine the quality of your product and help you achieve the desired image. Therefore, to understand more about DTG digital printing and the digital printing process, let’s take a look at the article below with EmbroInk!
What is DTG Digital Printing (Direct-To-Garment)?
In DTG (Direct to Garment) digital printing, also known as direct-to-fabric printing, is a method where images are printed directly onto fabric using inkjet technology and high-quality water-based ink. The water-based ink permeates deeply into the fabric fibers, ensuring vibrant and long-lasting colors.
This printing method excels in its ability to reproduce intricate and colorful designs on fabric. DTG printing offers precise detailing, consistency, unlimited print quantity, and cost-effectiveness, all maintained by skilled professionals in the field.
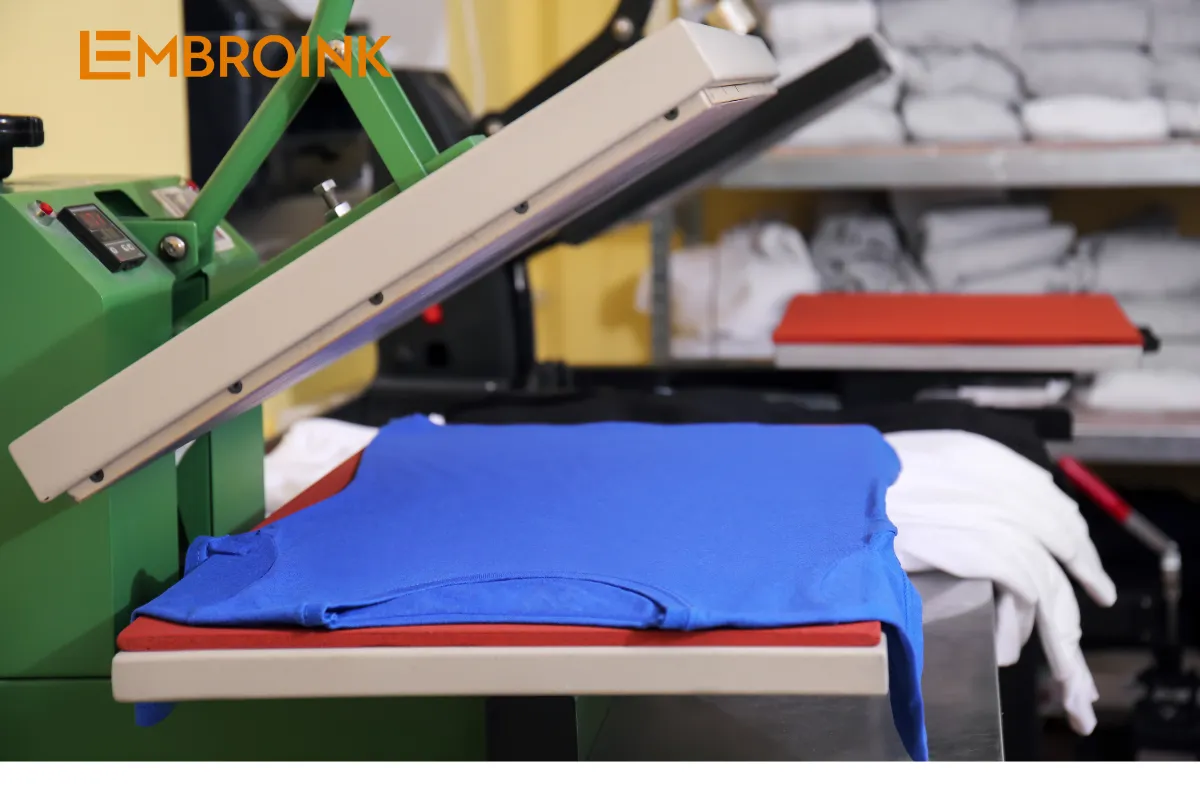
Advantages and disadvantages of Direct-To-Garment
Depending on your intended use, you should choose the printing method that best suits your needs. Below are the advantages and disadvantages of digital printing that you should be aware of:
Advantages
- Prints on various materials: such as fabric, paper, plastic, glass, ceramic, rubber, etc.
- High color fidelity and precision: One prominent advantage of digital printing is its extremely high accuracy and sharpness, producing lifelike images. This enhances the vividness and attractiveness of your designs. Additionally, the prints are highly durable, maintaining color vibrancy even after multiple washes.
- Time-saving: The printing process is fast, and the operational principles are straightforward. You can obtain prints within minutes without long waiting times.
- Versatility in image variety and sizes: You can easily change design files if errors occur and reprint immediately. Large-format digital printers can produce items in any desired size, from a few millimeters to several meters. Moreover, images can be segmented and easily pieced together.
Disadvantages
- High equipment investment costs: The major drawback of digital printing is the significant initial investment required for printing equipment. Additionally, if using Direct-To-Garment on certain difficult-to-print materials, specialized and modern equipment is necessary.
- Requires regular maintenance: For large-volume printing, regular machine maintenance is essential to ensure stable operation. Ink can also be prone to damage or clogging printheads.
- Higher production costs: Due to the use of high-quality inks, the cost of digital printing is generally higher compared to traditional methods such as screen printing or decals.
These factors should be carefully considered when choosing digital printing as your preferred method, depending on the specific requirements of your project or business.
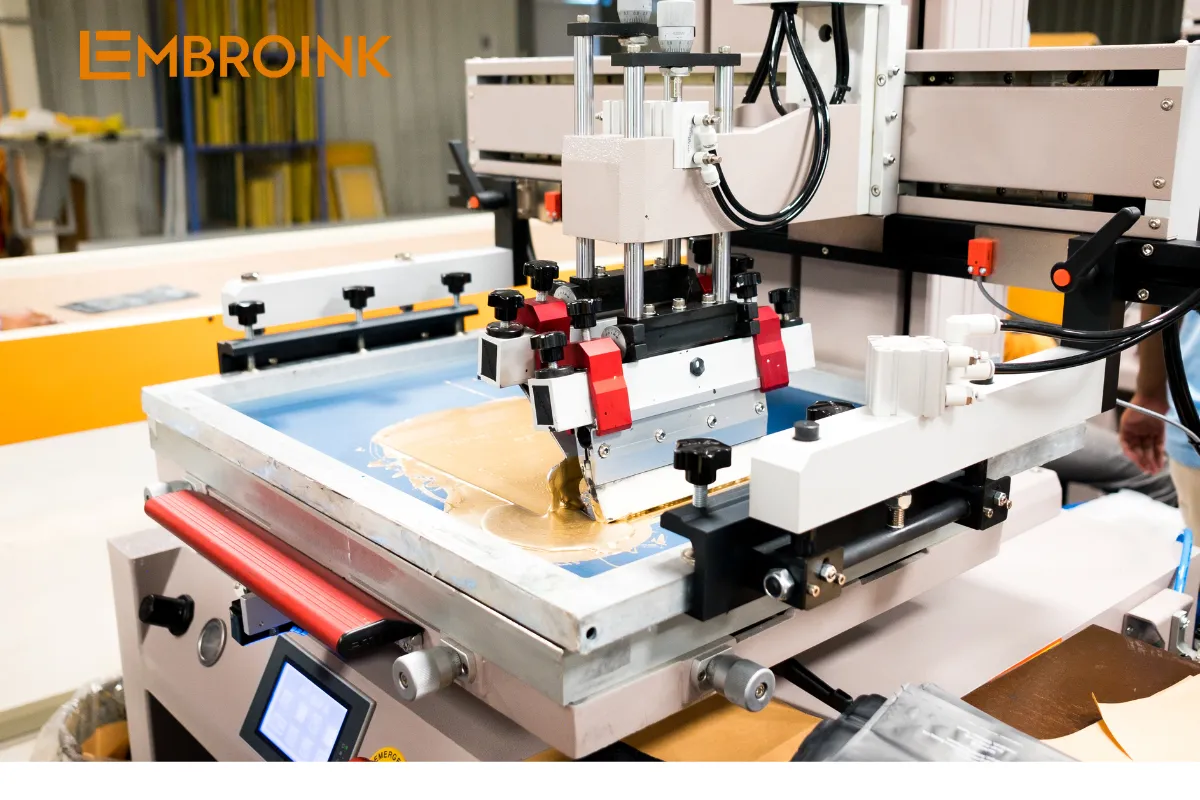
Applications of DTG Digital Printing
The applications of DTG digital printing are diverse and extensive. Here are three industries where digital printing is widely utilized:
Fashion industry
In the fashion and apparel industry, Direct-To-Garment is commonly used to print designs directly onto fabric and clothing. With DTG (Direct-To-Garment), entire designs can be printed in a single run. DTG printing does not limit the number of colors, so simply sending the print file ensures the request can be fulfilled.
Advertising industry, photo printing
In the advertising industry, digital printing is extensively used for printing images, billboards, flyers, posters, business cards, wedding invitations, and more. This printing technology has brought significant convenience and flexibility to advertisers and advertising material producers.
A notable feature of digital printing is its ability to directly print from electronic files without the need for plates or complex setup procedures required in traditional offset printing. This reduces production time, cuts costs, and efficiently facilitates small print runs. Moreover, the flexible editing capability of electronic files prior to printing is a major advantage, allowing easy changes to content, images, and colors.
The adoption of digital technology also opens up new creative opportunities in advertising design. Designers can explore a diverse range of visual elements and colors, creating impactful advertising materials that effectively capture customer attention.
Other Industries
Digital printing is also widely applied across various manufacturing sectors, particularly in decoration and interior design. This technology has revolutionized these industries by offering enhanced customization capabilities and efficient production processes.
In decoration, digital printing allows for intricate and personalized designs on various surfaces such as textiles, ceramics, glass, and wood. This versatility enables designers to create unique patterns, textures, and colors that traditional methods struggle to achieve. Whether it’s printing custom wallpapers, upholstery fabrics, or decorative tiles, digital printing offers unparalleled flexibility and precision.
In interior design, digital printing plays a crucial role in creating bespoke elements for residential and commercial spaces. It enables the production of custom murals, artwork, and signage that can transform interiors with vibrant visuals and detailed graphics. The ability to print directly onto materials like metal, acrylic, and PVC opens up endless possibilities for creating durable and visually striking interior decor elements.
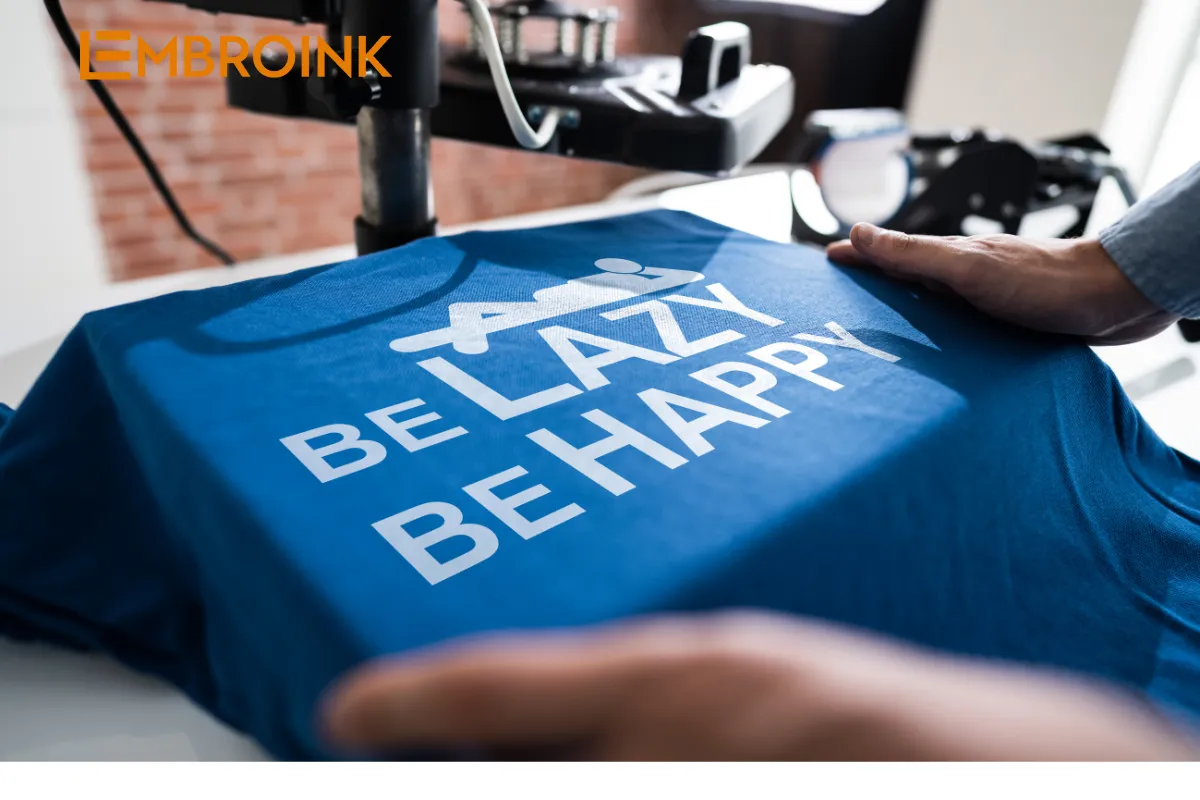
Best fabrics for digital printing
Digital printing methods are known for producing high-quality prints and fast production speeds. However, to enhance aesthetics and better meet consumer demands, it’s essential to choose the right fabric for digital printing. Here are some of the best fabrics for DTG (Direct-to-Garment) printing:
Digital printing on cotton fabric
Digital printing can directly spray colors onto cotton fabric without needing design adjustments. This method allows for very fast printing speeds while ensuring image quality and fabric integrity.
Cotton fabric has many advantages, making it widely used in the fashion industry. To achieve the highest quality digital prints on cotton fabric, most digital printers use reactive ink because it provides the best wash durability for prints on cotton.
Digital printing on silk fabric
Silk, known for its luxurious texture and natural sheen, offers a sophisticated canvas for digital printing applications. When considering printing on silk, the choice of ink plays a crucial role in achieving the desired outcomes.
Reactive ink is often preferred when durability is a primary concern. This type of ink forms a strong chemical bond with the silk fibers during the printing process. As a result, the prints exhibit excellent wash fastness and color retention over time, making them suitable for applications where the fabric will undergo frequent washing or wear.
On the other hand, acid ink is chosen for its ability to deliver vibrant and vivid colors. It penetrates silk fibers deeply, producing sharp and bright prints that stand out for their color intensity and clarity. This makes acid ink a popular choice in fashion and textile industries where vibrant color representation is paramount.
Viscose fabric
Viscose is a versatile fabric crafted from regenerated cellulose fibers sourced from plants such as bamboo, sugarcane, and soybeans. With a structure akin to cotton, it enjoys widespread popularity in fashion circles, particularly during the warm summer months.
When employing the DTG (Direct-to-Garment) method on viscose fabric, opting for reactive ink is highly advisable for achieving optimal results. Reactive ink interacts chemically with the cellulose fibers in viscose during printing, creating a durable bond that ensures excellent color retention and wash fastness. This makes it ideal for garments and textiles that require both vibrant prints and longevity against washing and wear.
The choice of reactive ink enhances the ability to reproduce intricate designs and vibrant colors on viscose fabric, catering to the demands of modern fashion trends and consumer preferences. By selecting reactive ink, manufacturers and designers can confidently produce high-quality printed viscose garments that combine aesthetic appeal with durability, meeting the expectations of discerning customers in the fashion industry.
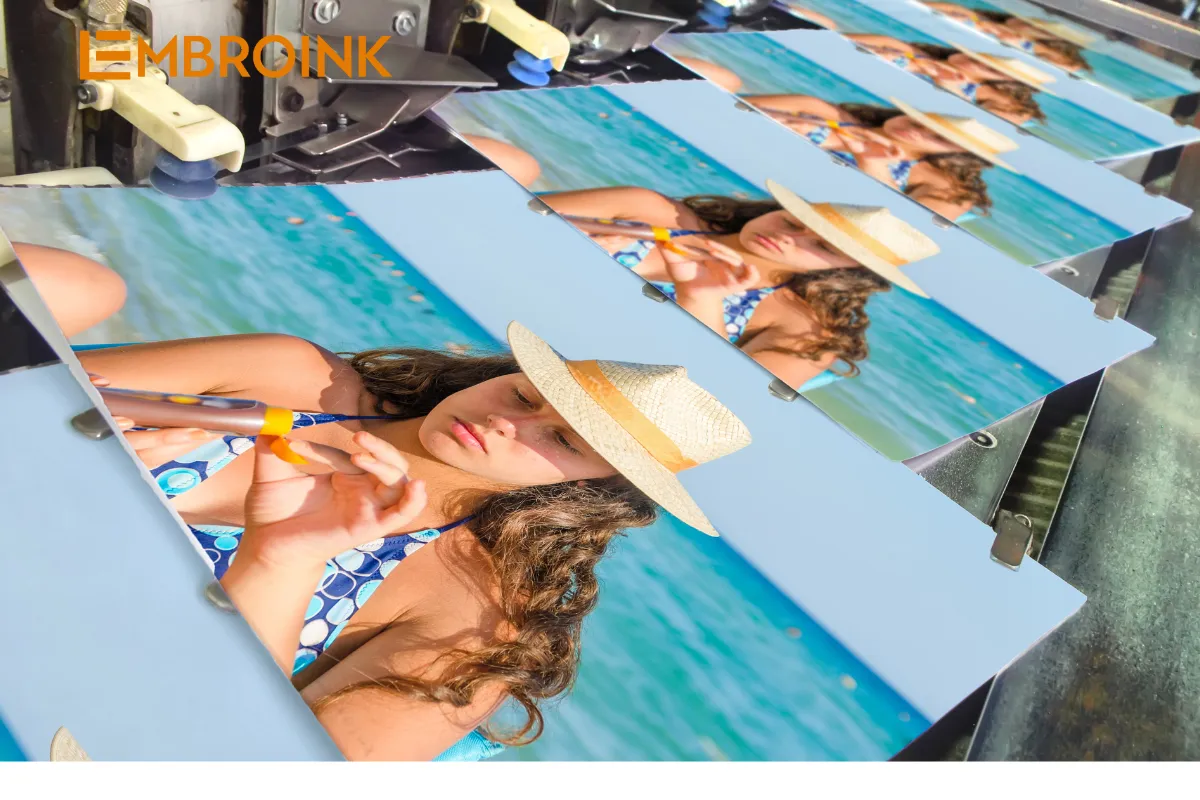
DTG Digital printing process
The operation of the digital printing method is based on the automation of machinery. The image to be printed is loaded into the digital printer from a computer, after which the machine analyzes the data and automatically mixes the ink to produce the final product immediately without much waiting time. The Direct-To-Garment process involves the following six main steps:
Step 1: Prepare the print file and load it into the DTG printer
Ensure that the print file is correctly prepared and then load it into the DTG printer.
Step 2: Prepare the printing material
Prepare the fabric for printing by heat pressing it to make the surface smooth. Before applying the ink, a pre-treatment liquid should be sprayed onto the fabric. Then, prepare the ink and load everything into the printer.
Step 3: Check the printer
Before printing, ensure that the fabric is laid completely flat in the printer. This will help avoid white gaps caused by wrinkles, which could ruin the entire printing process.
Step 4: Start the automatic printing process
If the preparation has been carried out properly and according to the printing process requirements, the automatic printing will proceed smoothly. Remember not to rush this process to ensure the desired quality.
Step 5: Dry the print
Once the printer produces the printed product, wait for the ink to dry. To save time, the printed item can be passed through a drying machine. Immediately after printing, gently remove the garment from the DTG printer.
Step 6: Inspect and finish the printing process
Inspect the quality of the print and the overall product. If everything is satisfactory, the printing process is completed and the product is ready to be delivered to the customer.
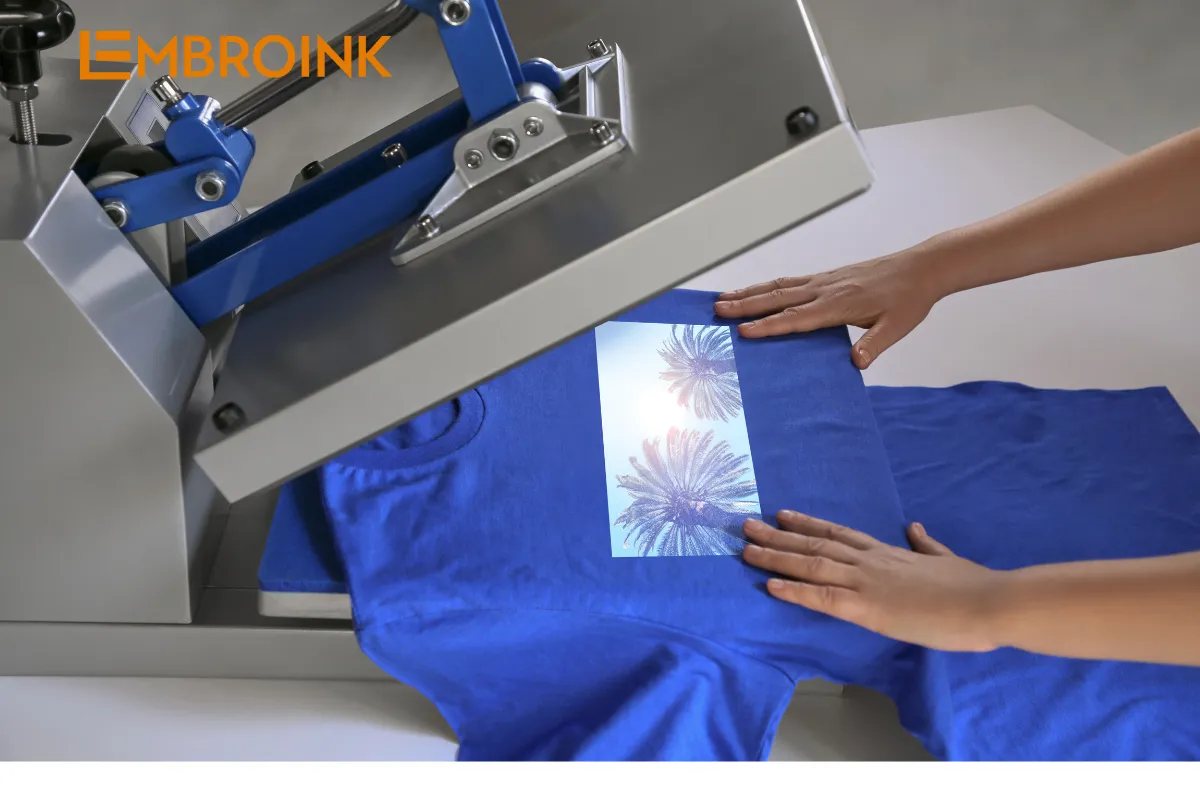
Tips for effective Direct-To-Garment
To achieve maximum efficiency in Direct-To-Garment, consider the following important tips:
- Choose the right dryer: Select a dryer with appropriate heat settings and drying times suitable for the type of printing material and ink used. This helps prevent issues like blurred or color-bleeding prints after drying.
- Avoid impact and mishandling: Handle printing materials with care to avoid impacts or mishandling that could compromise print quality. Ensuring a smooth surface without creases helps maintain sharp print output.
- Check and adjust technical specifications: Accurately adjust color settings to match the specific printer and printing technique. This includes balancing color tones and ink consistency on the fabric.
By adhering to these guidelines, you can ensure that the DTG printing process runs efficiently, resulting in high-quality prints that meet both standards and customer expectations.