How to prepare a file for DTF Printing: A comprehensive guide
Direct-to-film (DTF) printing emerged to overcome the limitations of direct-to-garment (DTG) printing, particularly in terms of material compatibility and color vibrancy. It gained popularity in the early 2000s and has since become widely adopted. The key benefits of DTF printing for custom clothing include long-lasting, vibrant, and sharp prints, along with its versatility on a wide variety of fabrics.
In this article, you’ll find valuable insights into DTF printing, step-by-step instructions for preparing print files, and tips to avoid common mistakes.
What is DTF Printing?
DTF (direct-to-film) printing uses water-based inks to print designs onto a specialized PET film. The design is then transferred to a garment using a heat press. This method produces durable and vibrant designs and works well on various fabrics.
Here’s how the DTF process works in real life for creating a print-on-demand shirt:
- Printing the Design: The design is printed onto the special transfer film using water-based inks.
- Applying White Ink: A layer of white ink is added on top of the design, which acts as a binder for the adhesive powder.
- Cutting the Film: The fulfillment specialist then cuts out the transfer film with your design.
- Heat Transfer: The film is applied to the garment and heat pressed to transfer the design from the film to the fabric.
Though DTF sounds similar to direct-to-garment (DTG) printing, there are key differences between the two methods. Here’s a 2-minute video that explains both techniques and offers a behind-the-scenes look at the process.
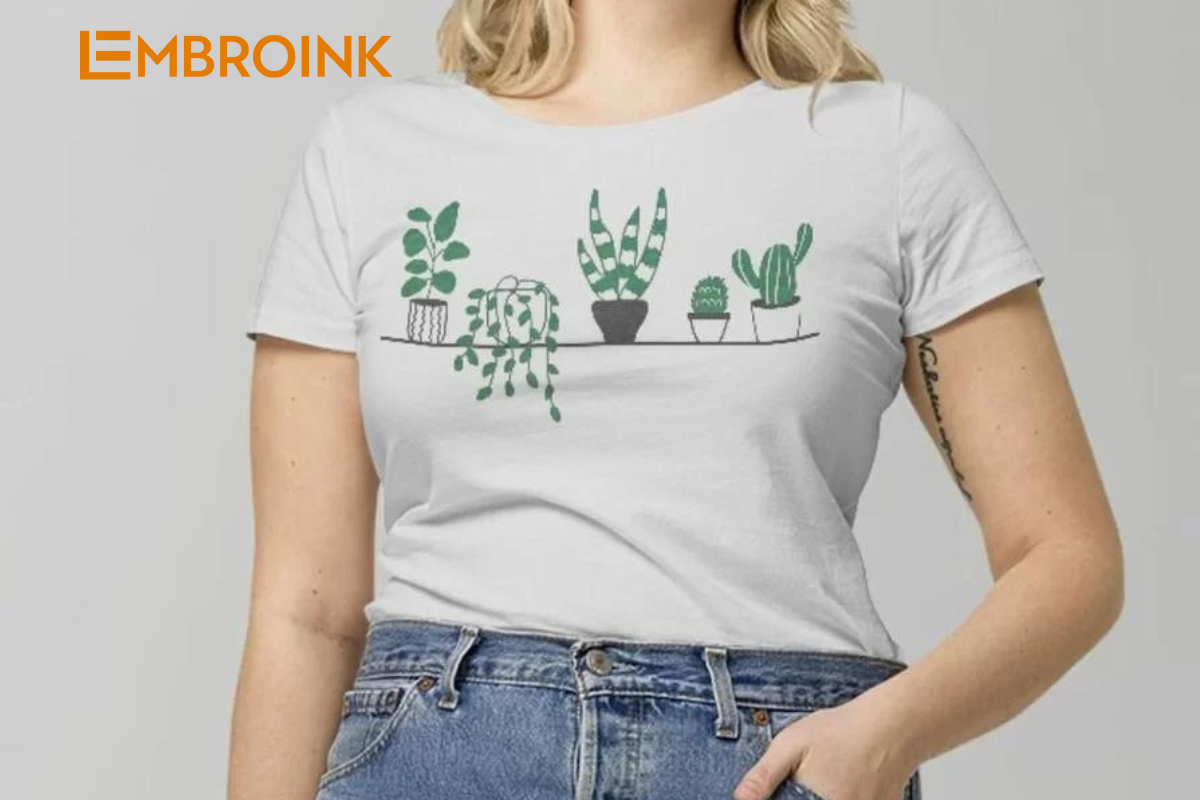
What Are the Differences Between Print Files for DTG and DTF Printing?
Although DTG and DTF printing techniques differ, the print file requirements for both are quite similar. However, when preparing files for DTF printing, here are a few design elements to avoid:
- Small Dots and Narrow Lines: These can peel off due to the limited area for adhesive application.
- Gradient Transitions: Avoid designs with gradients transitioning from solid to transparent or semi-transparent, as they can affect the print quality.
- Large Prints: Large designs covering a significant portion of the garment (especially on thin fabrics) can feel plasticky and reduce breathability.
By keeping these considerations in mind, you’ll ensure a more durable and comfortable final product when using DTF printing.
File Prep for DTF Printing: Best Practices
When preparing your files for DTF printing, following these best practices will ensure high-quality, durable prints. Here’s what you need to know:
Avoid Semi-Transparent Designs
Semi-transparent elements or graphics with lowered opacity don’t translate well in DTF printing because the process requires a solid, opaque layer of ink to adhere properly to the garment. When designs include transparency, the ink coverage becomes inconsistent, leading to patchy prints or colors that appear dull and washed out.
To achieve optimal results with DTF, it’s essential to use solid colors. Solid colors ensure that the ink is applied evenly and vibrantly, producing sharp, clean designs. Unlike transparent elements, which can create a blotchy or uneven finish, solid colors guarantee a more durable and visually striking print that remains vivid and detailed over time. Additionally, solid colors help the design stand out against various fabric types and colors, offering a more professional and polished look.
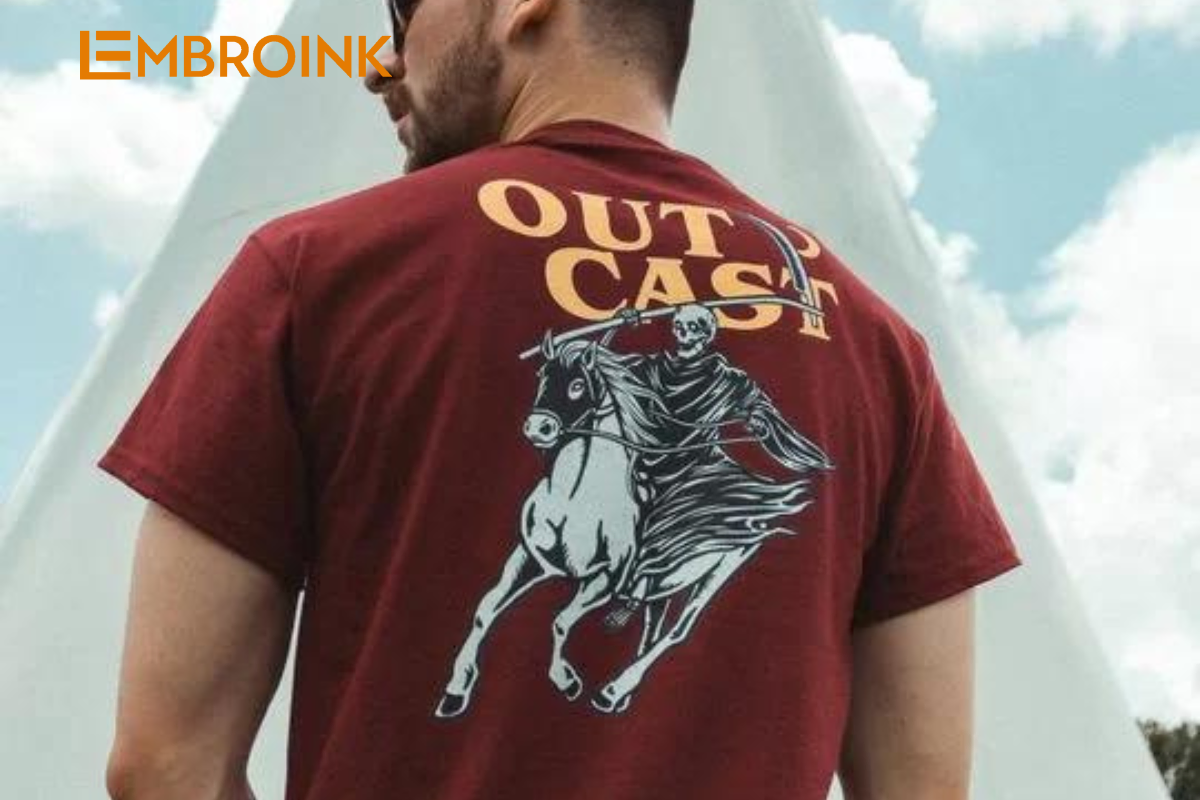
Incorporate See-Through Elements
Incorporating see-through areas in your DTF designs can enhance both the look and feel of your printed garment. By strategically leaving open spaces in the design, you reduce the amount of ink and adhesive applied, which results in a lighter, more breathable print. This approach is particularly beneficial when working with large designs, as it avoids the stiffness that can occur when covering large sections of fabric with solid prints.
Not only does this technique improve the comfort of the garment, but it also gives the design a more dynamic and modern aesthetic. The lighter print feels softer against the skin and ensures the fabric retains its natural flexibility, making it a more comfortable choice, especially for everyday wear.
Ensure Proper DPI
DPI (dots per inch) is crucial for achieving high-quality prints. To ensure your designs are sharp and detailed, aim for a resolution between 150 and 300 DPI. Higher DPI values contribute to greater clarity and precision in the final print.
Simply adjusting the resolution of a low-quality graphic will not enhance its clarity. If the original design has a low resolution, the best approach is to recreate the design at a higher resolution to meet the required DPI. This ensures that the details are crisp and the print is vibrant and professional.
Use PNG or JPEG Formats
Submit your files in either PNG or JPEG format, and make sure the image resolution is within the recommended 150–300 DPI range. This ensures that your print will be sharp, clear, and of high quality.
Avoid Soft Edges in Designs
Designs with soft or feathered edges can pose significant challenges in DTF printing. The small ink dots used to create these soft transitions often have difficulty adhering consistently, resulting in rough or blotchy edges. This is because the gradient or feathered effect relies on very fine, delicate areas of ink, which may not hold up well under the adhesive layer and heat transfer process.
To achieve cleaner, more professional results, it’s best to use crisp, defined edges in your designs. Sharp, well-defined lines and shapes ensure that the ink adheres properly and maintains its integrity throughout the printing and transfer process. This approach helps avoid issues like blurriness or uneven application, resulting in a more precise and visually appealing print.
Use High-Resolution Images for Customization
DTF printing is particularly well-suited for full-color photography designs, offering exceptional detail and vibrancy. To achieve the best results, it’s crucial to use high-resolution images. High-resolution files ensure that every detail is captured and reproduced clearly, resulting in sharp, vivid prints that accurately reflect the original image.
When preparing your images for DTF printing, always choose the highest quality available. This not only enhances the visual appeal of the final product but also ensures that intricate details and color gradients are faithfully represented, providing a professional and polished look.
Stick to the sRGB Color Profile
The sRGB IEC61966-2.1 color profile is essential for ensuring that colors are represented consistently and accurately across various devices and printers. By using this color profile, you maintain color integrity from design to print, reducing the risk of discrepancies and ensuring that your designs look as intended.
However, it’s important to note that extremely bright or saturated colors might appear slightly less vibrant due to the limitations of the printing process. Despite this, sRGB remains the best choice for achieving the most accurate color reproduction possible, ensuring that your prints are as true to your original design as the technology allows.
By following these guidelines, you’ll maximize the quality and longevity of your DTF prints.
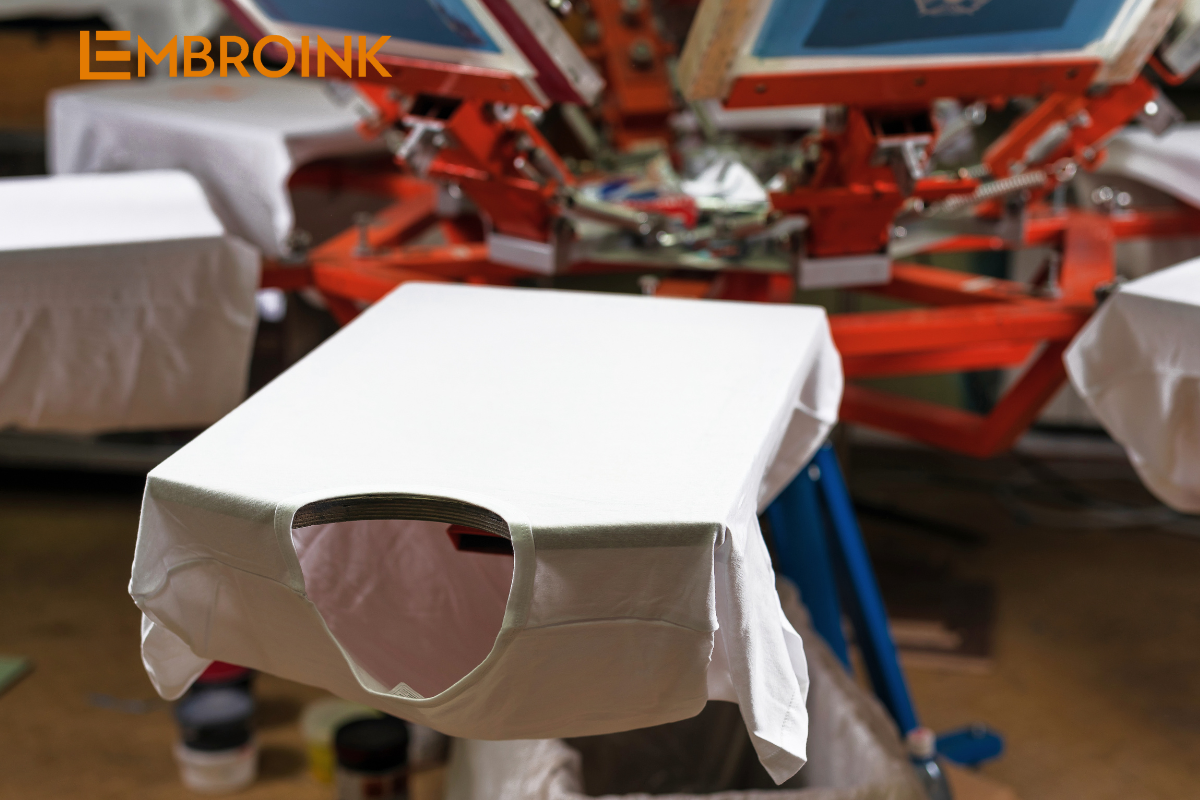
Most Common Mistakes in DTF Printing
To ensure the best possible results for your DTF-printed garments, it’s important to know what to avoid. Here are some common mistakes that can lead to poor-quality prints:
- Poor Print File Quality: DTF printing relies on sharp, crisp lines. Files with a resolution lower than 150 DPI can result in blotchy, uneven edges or unclear prints. Always ensure your design meets the resolution requirements.
- Too Many Small Details: Tiny elements like dots and thin lines tend to peel off over time due to the limited adhesive coverage. Avoid intricate designs with excessive small details to maintain durability.
- Large Solid Print Areas: Large solid print areas can feel stiff and reduce the garment’s breathability. To avoid this, consider incorporating see-through elements or reducing the size of solid prints.
- Black Design on Black Fabric: Black prints on black fabrics often appear dull or greyish. It’s best to avoid black-on-black designs to prevent the print from blending into the fabric and losing vibrancy.
- Gradient from Solid to Transparent: Gradients that transition from solid to transparent are created using small dots, which, as mentioned, don’t adhere well. Avoid this design feature to maintain print quality.
By steering clear of these common pitfalls, you can ensure that your DTF prints are vibrant, long-lasting, and of the highest quality.
How to Take Care of Your DTF Printed Garments
While DTF prints are known for their durability, proper care is essential to extend the life of your printed garments. Here are some tips to keep your DTF prints looking great:
- Wash in Cold or Lukewarm Water: Always wash DTF-printed garments in cold to lukewarm water. This helps prevent the print from cracking or fading over time.
- Avoid Hot Water: Never wash your garment in hot water, as the heat can cause the print to crack and deteriorate.
- Turn the Garment Inside Out When Ironing: When ironing, make sure to turn the garment inside out to protect the print from direct heat.
By following these simple steps of EmbroInk, you can ensure that your DTF prints remain vibrant and last longer.