How to order embroidery on demand: Maybe you don’t know
Embroidery on demand has become a popular trend in the world of fashion and interior decoration. Not only does it produce unique and personalized items, but it also showcases the creativity and individual style of the customer. Above all, custom embroidery brings satisfaction and pride in owning products that bear one’s own personal touch.
In this section, let’s delve deeper into the process and considerations when placing custom embroidery orders, from pre-order preparation to execution and post-completion product care, with EmbroInk.
Things to prepare before laying embroidery
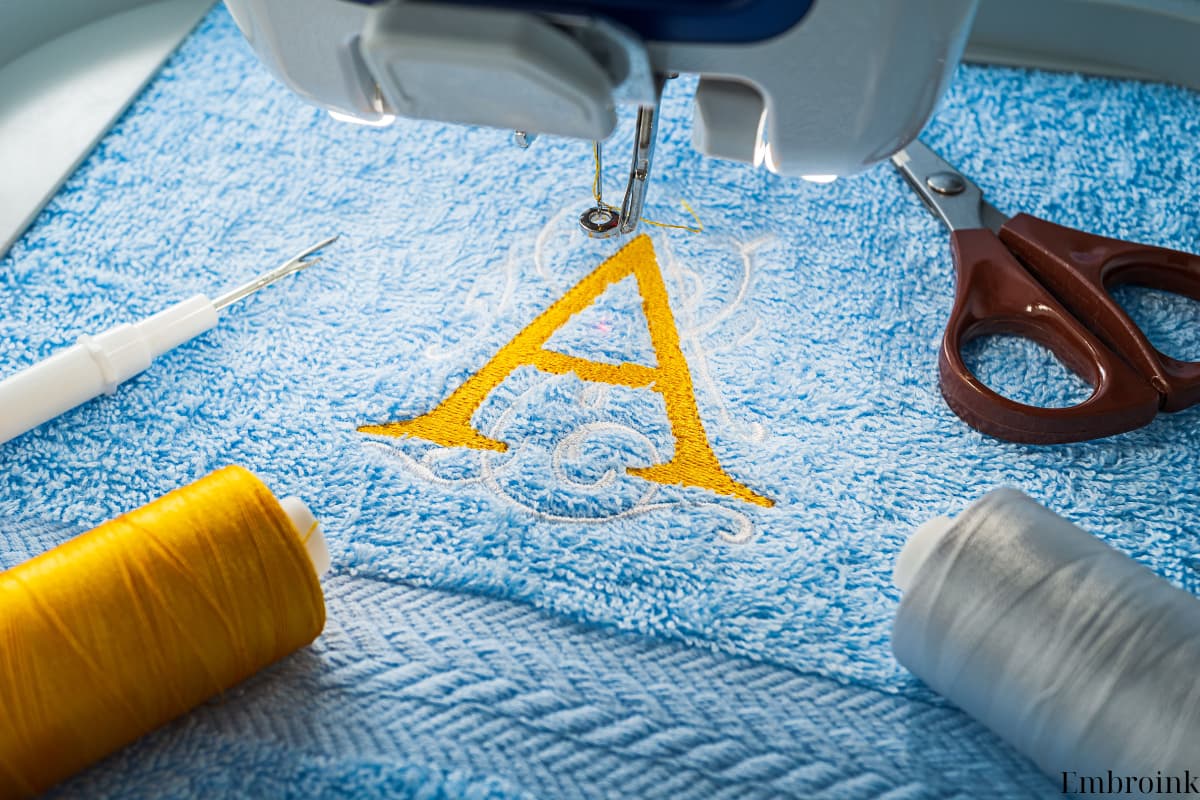
Before embarking on the embroidery on demand ordering process, thorough preparation is crucial to ensure that you receive the desired product. Below are some key considerations during this preparation phase:
Choose a design template
- Clarify the idea and purpose of the embroidered product: Before selecting a design, it’s essential to clearly define the purpose of the embroidered product. It could be for embellishing clothing, pillows, tablecloths, or even wall decorations. This idea will help you choose a design that suits your needs and desires.
- Search and select a suitable design: Once you’ve determined the purpose, you can search for design patterns on embroidery websites, in books or reference materials, or even create your own design from your ideas. Choose a design that you like and best reflects your personal style, as well as suits the product you want to embroider.
- Assess the feasibility of the design: Before deciding on the final design, assess its feasibility. This includes considering the embroidery technique to be applied (such as hand embroidery, machine embroidery, or appliqué embroidery), the complexity of the design pattern, as well as the ability to select suitable materials and colors for the design.
By doing so, the process of selecting a design will become easier, ensuring that you will receive an embroidered product that meets your expectations.
Materials and colors
Firstly, you need to consider the type of fabric that best suits your embroidery project. For clothing, you may choose fabrics like cotton, linen, or satin depending on the intended use and design style. For interior decoration, you might opt for silk or heavy-duty fabrics like canvas.
The choice of fabric colors and materials is crucial in creating a visually appealing embroidered product that accurately reflects your ideas. Select colors that complement the style and space you intend to embroider. Additionally, ensure that the chosen fabric material aligns with the type of embroidery you plan to apply (for example, soft and flexible fabric for hand embroidery, sturdy and durable fabric for machine embroidery).
Embroidery size and position
Before commencing embroidery, it’s crucial to ascertain the exact dimensions of the product. This ensures that the design will accurately reflect on the surface you intend to embroider. Take meticulous measurements and determine the width, height, and any other technical details necessary to ensure maximum accuracy.
You need to decide on the specific placement on the product you want to embroider before starting the embroidery process. This includes pinpointing the exact location on the product’s surface as well as determining other factors such as distance from edges, coordination with other elements of the design, and convenience in executing the embroidery process.
Before proceeding with embroidery, ensure that the placement and dimensions have been determined to be practical and best reflect your ideas and design. Make any necessary adjustments to ensure that the embroidered product will meet your expectations.
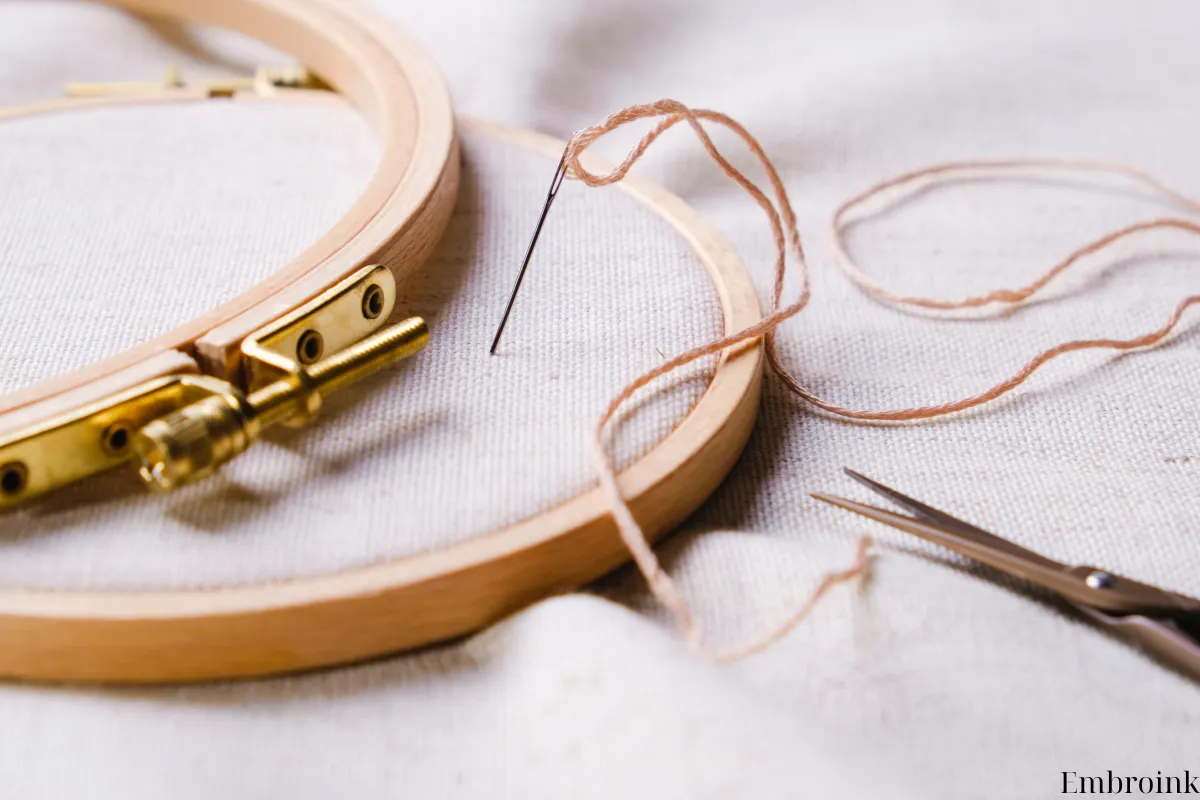
Choosing the right type of embroidery
Hand embroidery
- Characteristics: Hand embroidery is the process of stitching designs by hand, typically using a needle and thread to create patterns and images on fabric. This type of embroidery is highly artistic, allowing the embroiderer to freely express their creativity and skills.
- Advantages: Hand-embroidered products often have high quality and a high degree of personalization, as they are meticulously crafted.
It allows for the addition of intricate and unique details to the design. - Disadvantages: It requires more time and effort compared to machine embroidery. The cost is usually higher due to the time and labor involved.
Embroidery Machine
- Characteristics: Machine embroidery uses automated embroidery machines to create patterns and images on fabric. This process is quick and efficient, making it suitable for mass production.
- Advantages: Saves time and effort compared to hand embroidery. Ideal for projects that require large quantities of products or need to be completed quickly.
- Disadvantages: Limited in expressing intricate details and personalization compared to hand embroidery. Can sometimes result in technical errors due to mechanical factors.
Appliqué Embroidery
- Characteristics: Appliqué embroidery is the process of stitching fabric pieces onto a base fabric to create patterns and images.
It is commonly used for artistic decoration projects and fashion. - Advantages: Allows creativity and versatility in material usage. Creates 3D effects and distinctive styles for the product.
- Disadvantages: Requires high technical skill and experience in handling materials and appliqué. Execution time may be longer and demands patience and high skill level.
Contact the embroidery on demand address
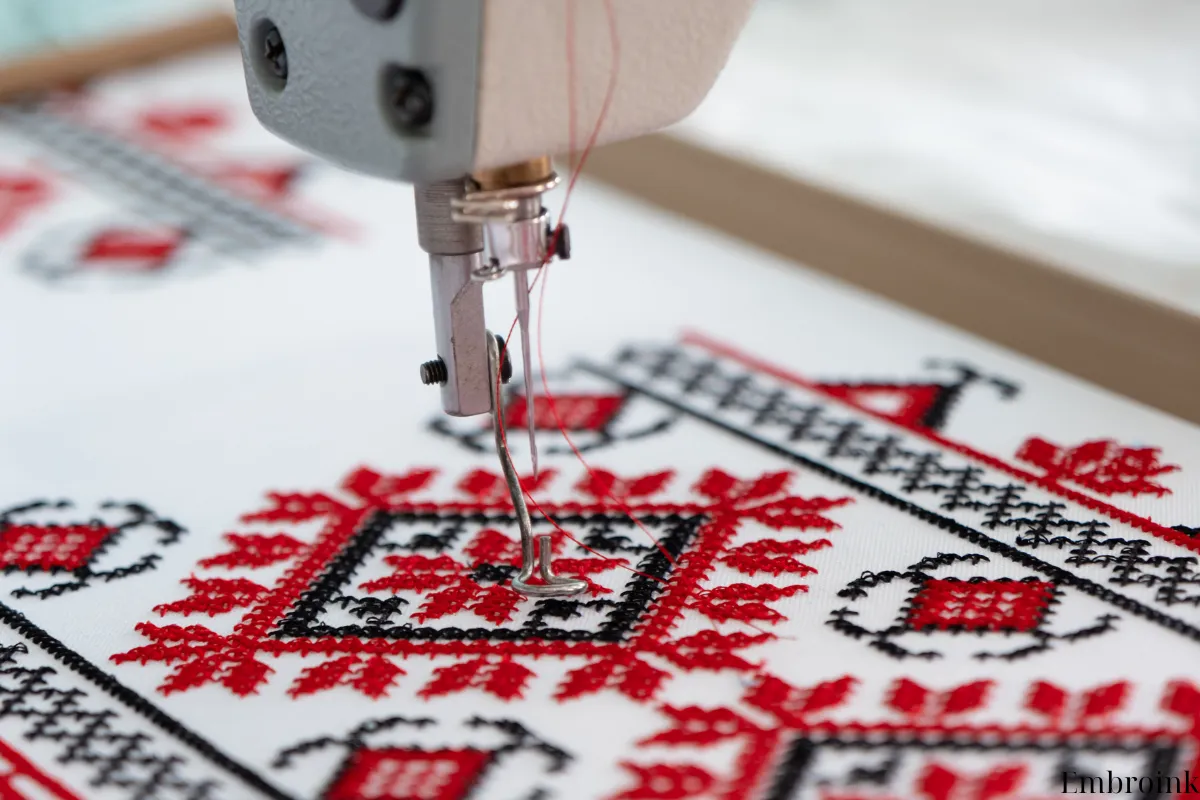
To initiate the embroidery on demand process, it’s crucial to communicate your request and negotiate with the embroidery service. This ensures that both parties understand the necessary details and reach a mutually agreed-upon arrangement. You can contact the embroidery service directly via email, phone, or in-person meeting to discuss the design, materials, colors, dimensions, and any other requirements. During negotiations, discuss pricing, turnaround time, and other terms such as deposits and return policies. Ensure that both parties fully understand and agree to the terms and conditions before commencing the embroidery project.
Implementation Process
The embroidery on demand implementation process requires precision and attention to detail from preparation to product completion. Here are the basic steps of the implementation process:
Design and Preparation
To create the design template on the fabric or embroidery material according to the request, this process demands accuracy and attention to detail from material selection to pattern positioning and conversion.
Firstly, it’s crucial to carefully select and prepare the embroidery materials. This includes choosing the appropriate fabric for the project, especially one with the necessary stiffness or loft to ensure the design becomes clear and easy to embroider. Additionally, it’s essential to select suitable threads that match the fabric type and color of the embroidered product.
Next, the process of preparing the design template requires meticulousness and technical skill. Use the provided design template or create a new one based on the client’s ideas. If there’s no existing template, this process typically starts with hand-drawing or using graphic design software to create a digital design template. Then, the design template is transferred onto the fabric or embroidery material using an embroidery pen or transfer paper. This process demands accuracy in positioning and converting the design template from a technical form to a real-life application on the fabric.
Embroidery Pattern
The next step after preparing the design template is to begin the process of embroidering the pattern on the fabric. This process requires high concentration and precise stitching skills to accurately reproduce each detail according to the prepared template. Below are the methods of execution for the two main techniques: hand embroidery and machine embroidery.
- Hand Embroidery:
Hand embroidery technique demands skillfulness and patience. Embroiderers use needles and threads to stitch natural lines or intricate stitches, creating patterns and small details following the design template.
For hand embroidery, the most important aspect is ensuring accuracy and precision in every stitch and detail. Embroiderers need to focus on faithfully reproducing the design template on the fabric, ensuring that every detail is impeccably executed.
- Machine Embroidery:
In the case of automated machine embroidery, the embroidery process becomes faster and more efficient. The embroidery machine automatically executes stitches and patterns according to the pre-set design template.
However, to ensure accuracy and precision, appropriate settings need to be selected on the embroidery machine, and the embroidery process needs to be carefully controlled. This includes ensuring that the threads are stitched in the correct position and depth to create sharp details.
Whether using hand embroidery or machine embroidery, ensuring accuracy and precision in executing the details of the design template is crucial. Even a small deviation can affect the quality and aesthetic appeal of the final embroidered product. Therefore, concentration and meticulousness in the embroidery process are indispensable.
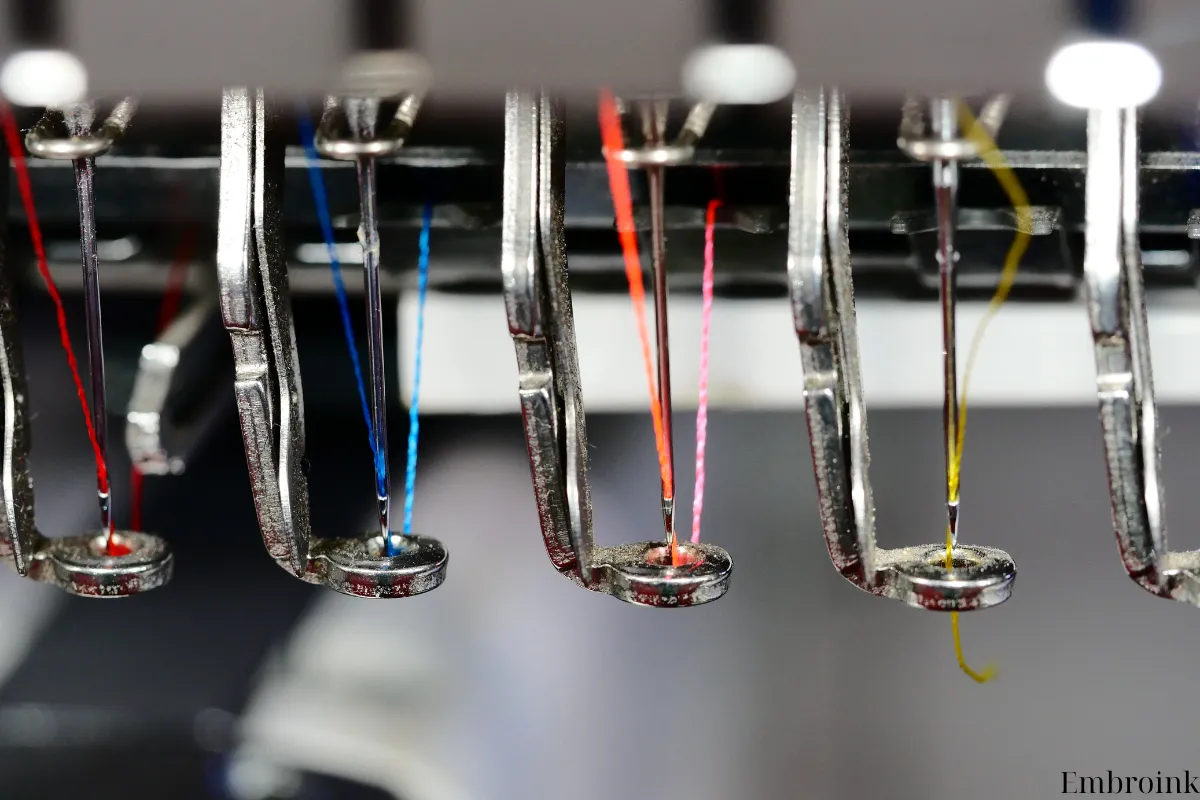
Inspection and Editing (if necessary)
After completing the embroidery process on the fabric, inspecting and adjusting the product is an essential step to ensure the highest quality and meet the customer’s requirements. This process begins with a thorough inspection of the entire embroidered product, where each stitch and embroidery point is carefully examined to identify any errors.
Next, the embroidered product is compared to the original design template to ensure that every detail is accurately reproduced as expected. It is especially important to pay attention to small and intricate details of the design template to ensure they are embroidered accurately and sharply.
In the event of any errors or mistakes detected in the embroidered product, corrective measures or adjustments will be promptly made. Broken stitches, uneven embroidery points, or missing details will be adjusted using either hand embroidery or machine embroidery techniques, depending on the specific requirements of the project.
The implementation process must be carried out with care and accuracy to ensure that the final embroidered product meets the highest quality and customer satisfaction.
Production and shipping time of Embroink
After completing and adjusting the embroidered product according to the requirements, the next step is to finalize and deliver the product to the customer. This process involves important steps such as trimming and cleaning the product to remove any excess thread, making the product neater and sharper. Additionally, re-inspecting the product before packaging is crucial to ensure that no defects are present and that every detail meets the highest quality standards.
Next, the embroidered product will be carefully and securely packaged to protect it during transportation and storage. Choosing appropriate packaging materials such as plastic bags, cardboard boxes, or fabric pouches also plays a crucial role in ensuring that the product remains intact during transportation.
Finally, the embroidered product will be delivered to the customer according to the agreed-upon location and delivery time. This needs to be done safely and punctually, accompanied by providing usage and care instructions if necessary. The process of finalizing and delivering the product not only marks the end of the production process but also provides an opportunity to make a positive impression and enhance the relationship with the customer.
Our goal is to process your orders promptly and efficiently:
- Production Time: 1 to 2 business days depending on the product and order complexity.
- Tracking Information: Tracking numbers are provided within 2 days of receiving payment for that orders. Tracking becomes active once the shipment reaches the destination country.
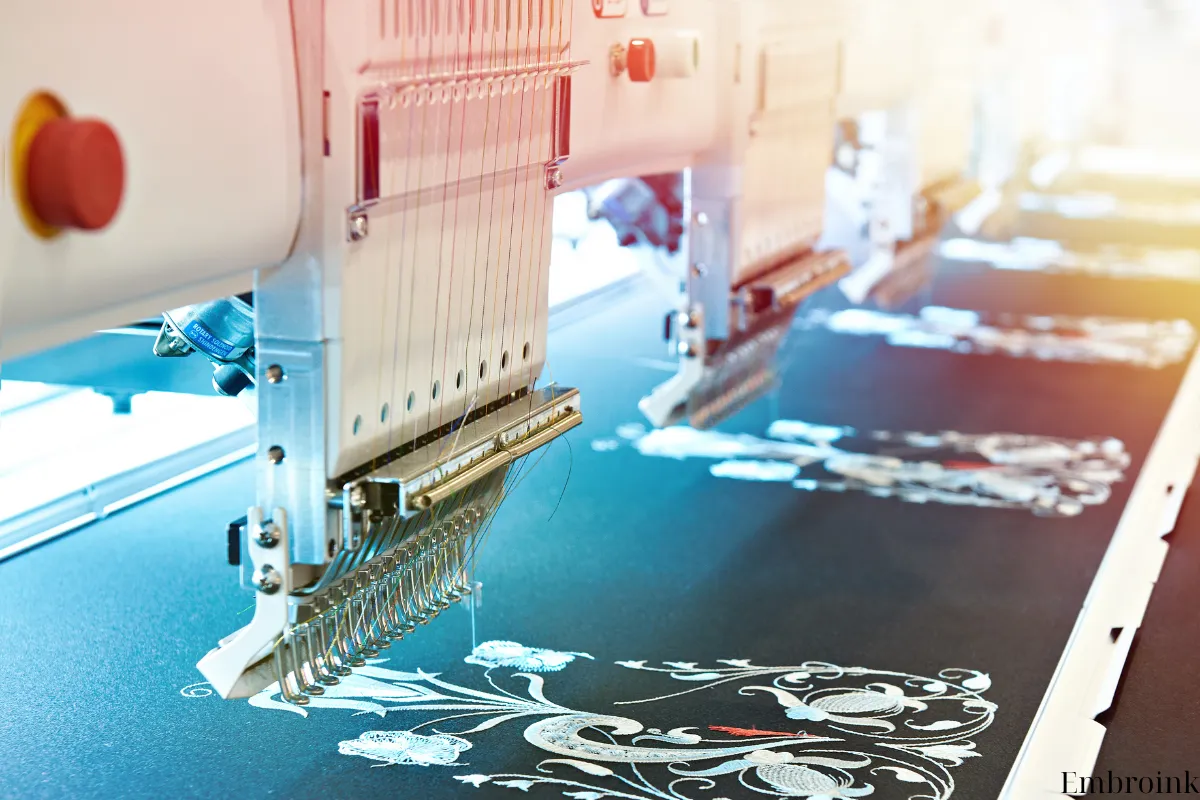
Estimated Shipping Time:
- US: Approximately 3 to 9 business days.
- UK & EU: Approximately 10 to 14 business days.
- *Orders to the EU that want to include tax will add $7 (orders need to have the consignee’s phone number and email)
- Other Countries: Approximately 21 to 30 business days.
Please note that delays may occur due to factors beyond our control such as customs delays or logistical issues. In such cases, while we will assist in resolving the issue with the carrier, we cannot guarantee immediate resolution.
Commitments of Embroink
Embroink is dedicated to providing the highest level of service, but there are certain situations where we cannot be held liable:
- We do not assume responsibility for orders if customers directly modify addresses with carriers.
- We are not responsible for inaccuracies in shipping addresses provided by the buyer.
- Customs fees or taxes are not covered by us; sellers are responsible for informing their customers about potential duties.
- If a customer refuses to pay customs duties and the order is returned, we do not refund these costs.
- We cannot address issues with orders claimed as undelivered if tracking information confirms delivery. (However, we are willing to collaborate with the shipping company to request maximum evidence)
Regarding Product Issues and Resolutions:
- To efficiently address product-related concerns, we require:
- A photo of the shipping label.
- Clear images of defects for items such as incorrect sizes, colors, or defective merchandise.
- Complaints must be lodged within 30 days of product delivery.
- For embroidery products, please be aware that ink marks from the design process are normal and will wash out. We consider this as non-defective.
- If a product is determined to be defective, and the fault lies with us, we will either resend the product at no extra cost or provide a refund of the base cost.