Essential information about Direct to Film Printing
Direct-to-film (DTF) printing is currently one of the most versatile techniques in the print industry. Unlike most print methods that are limited to similar fabrics like cotton and cotton blends, DTF printing allows you to work with tougher fabric varieties such as polyester, fleece, nylon, and, of course, classic cotton.
Read on to learn more about the DTF printing process and how it compares to other printing methods.
What is DTF Printing?
DTF (Direct-to-Film) printing is an innovative technique that involves several key steps to produce detailed and vibrant designs. Here’s how it works:
- Design Printing: A design is printed onto a piece of PET film, which is specially coated to aid in the transfer process.
- Ink and Adhesive Application: Water-based inks are used to print the design on the PET film. A special adhesive powder is then applied to the printed film.
- Heat Transfer: The PET film with the design and adhesive is heat-transferred onto fabric using a heat press machine.
This method ensures durability and produces high-quality, detailed, and vibrant designs suitable for various fabric types.
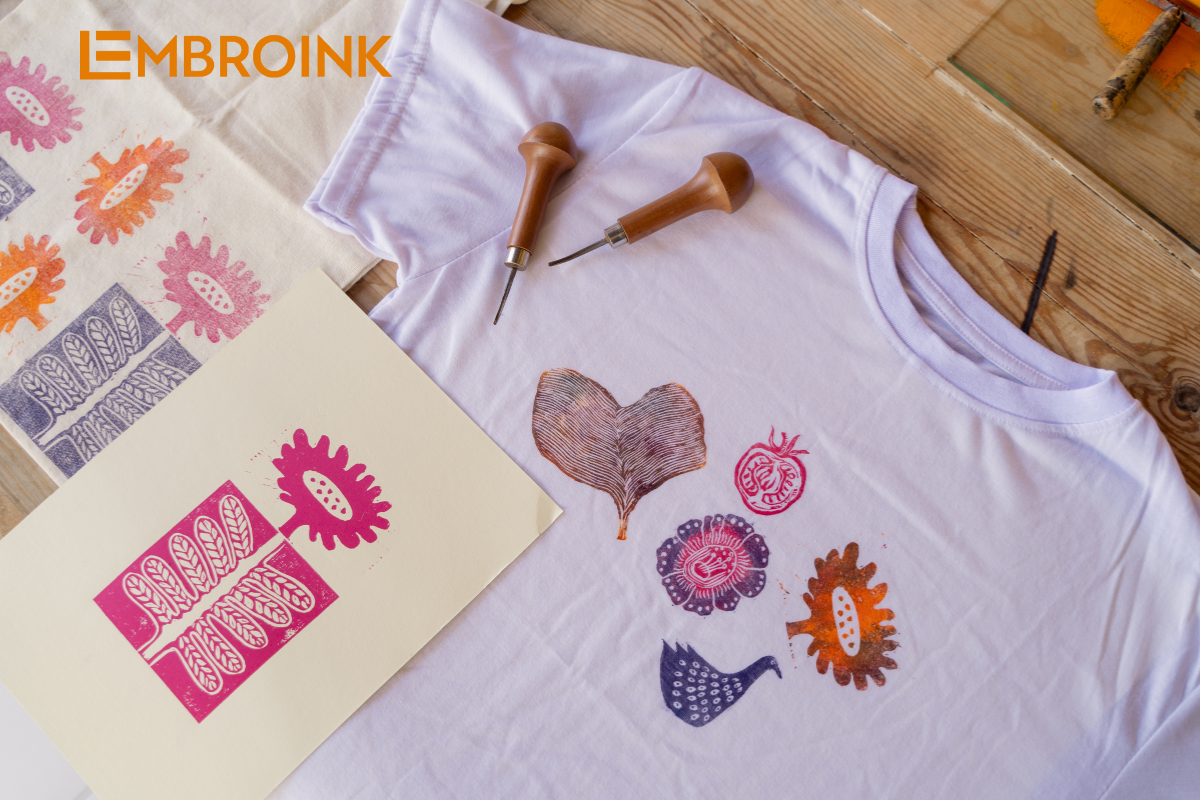
How does DTF Printing work?
DTF printing is a quick and efficient method, ideal for detailed designs on bulky, outdoor apparel. Here’s a step-by-step breakdown of the process:
Step 1: Preparing the Film
- Film Placement: A PET film is placed in the DTF printing machine, where the entire design is printed in color.
- White Layer Application: After the first layer is created, the machine prints a white layer over the entire image, completely covering the first layer. This ensures opacity and vibrancy of the final design. (Check out the image below to see how DTF print designs look once printed on PET film.)
Step 2: Pre-Pressing Fabric and Using a Heat Press
With the PET film preheated, the fabric receiving the design goes through the following steps:
Pre-Pressing the Fabric:
- Dehumidification and Flattening: The fabric is dehumidified and pre-flattened by being kept under heat for 2 to 5 seconds inside the heat press machine.
Transferring the Design:
- Placement: The printed film is placed on the pre-pressed fabric.
- Heat Press: The design on the film is then transferred to the garment using a heat press for 15 to 20 seconds at an average temperature of 165°C.
This process ensures that the design adheres well to the fabric, resulting in a durable and vibrant print.
Step 3: Peeling the Film and Post-Pressing the Fabric
With the design transferred onto the fabric, the final steps are as follows:
Peeling the Film:
- Cold Peel: Carefully peel the PET film away from the fabric once it has cooled. This ensures that the design remains intact and adheres properly to the fabric.
Post-Pressing the Fabric:
- Flattening: The designed fabric is flattened a second time in the heat press to improve the design’s durability and ensure it is securely bonded to the fabric.
After post-pressing, the garment is ready to be packed and shipped to customers.
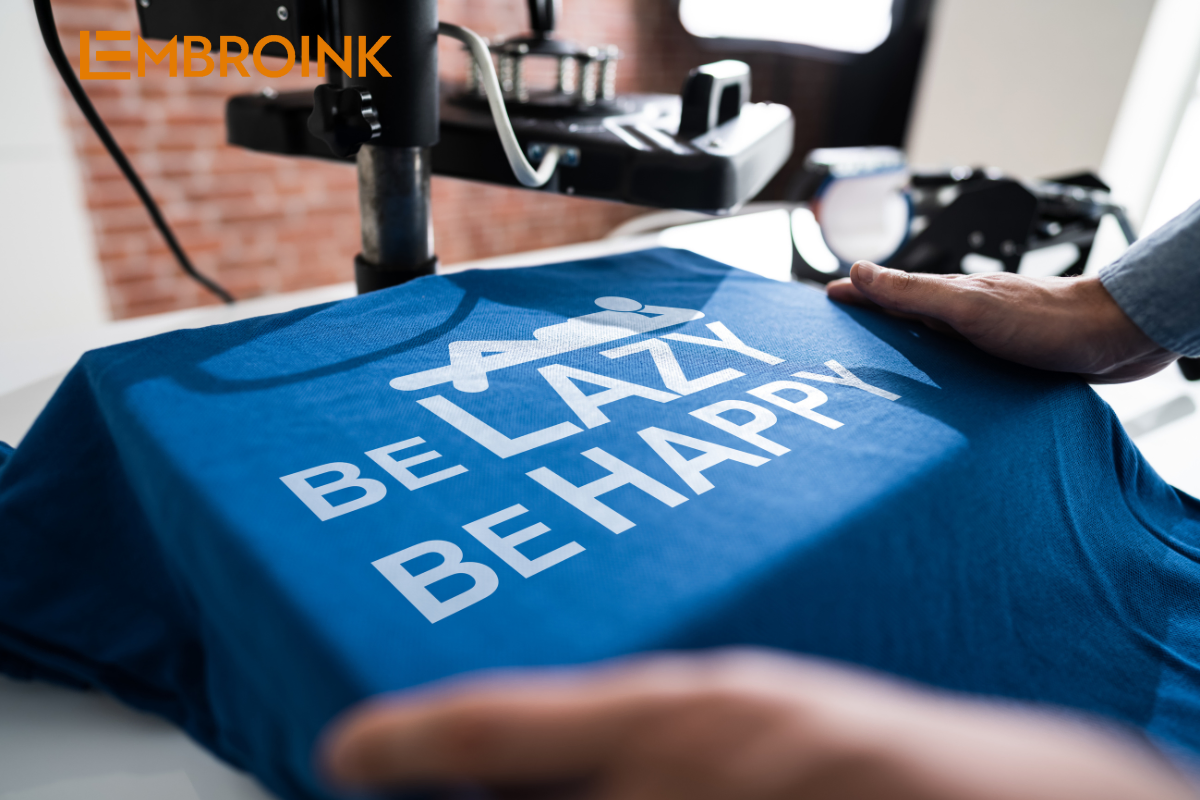
DTF Printing compared to other print methods
When choosing a printing method for your business, it’s crucial to align with your long-term goals and product selection. Here’s a comparison of DTF printing with other popular techniques:
Direct-to-Film vs. Screen Printing
Screen Printing:
- Process: Involves pushing ink through a woven screen or mesh stencil layer by layer onto fabric.
- Setup: Requires a separate screen for each color and design element.
- Resulting Feel: Ink lays on top of the fabric, creating a textured feel, especially with detailed designs that require more ink layers.
- Best Suited For: Solid designs without intricate details, such as symbols or geometric shapes.
DTF Printing:
- Process: Involves printing a design on PET film with water-based inks and an adhesive powder, then heat-transferring it to fabric.
- Setup: Does not require separate screens for each design; only needs a printer, transfer film, printing powder, and heat press.
- Resulting Feel: Offers a uniform feel on the fabric, regardless of the complexity of colors or design elements.
- Best Suited For: Detailed designs and various fabric types, including polyester, fleece, nylon, and cotton blends.
Direct-to-Film vs. Direct-to-Garment Printing (DTG)
DTG Printing:
- Process: Involves spraying water-based inks directly onto fabric after applying a pre-treatment solution.
- Fabric compatibility: Works best on cotton and cotton blends.
- Best suited for: Products primarily made of 100% cotton or cotton blends.
Conclusion:
- Use case: DTF printing is versatile for detailed designs and various fabric types, including polyester and blends, offering a uniform feel without the need for multiple screens.
- Considerations: If your product catalog includes a mix of fabric types and intricate designs, DTF printing can complement DTG printing’s strengths in handling cotton-based apparel.
Understanding these distinctions will help you choose the best printing method to match your brand’s product offerings and market needs effectively.
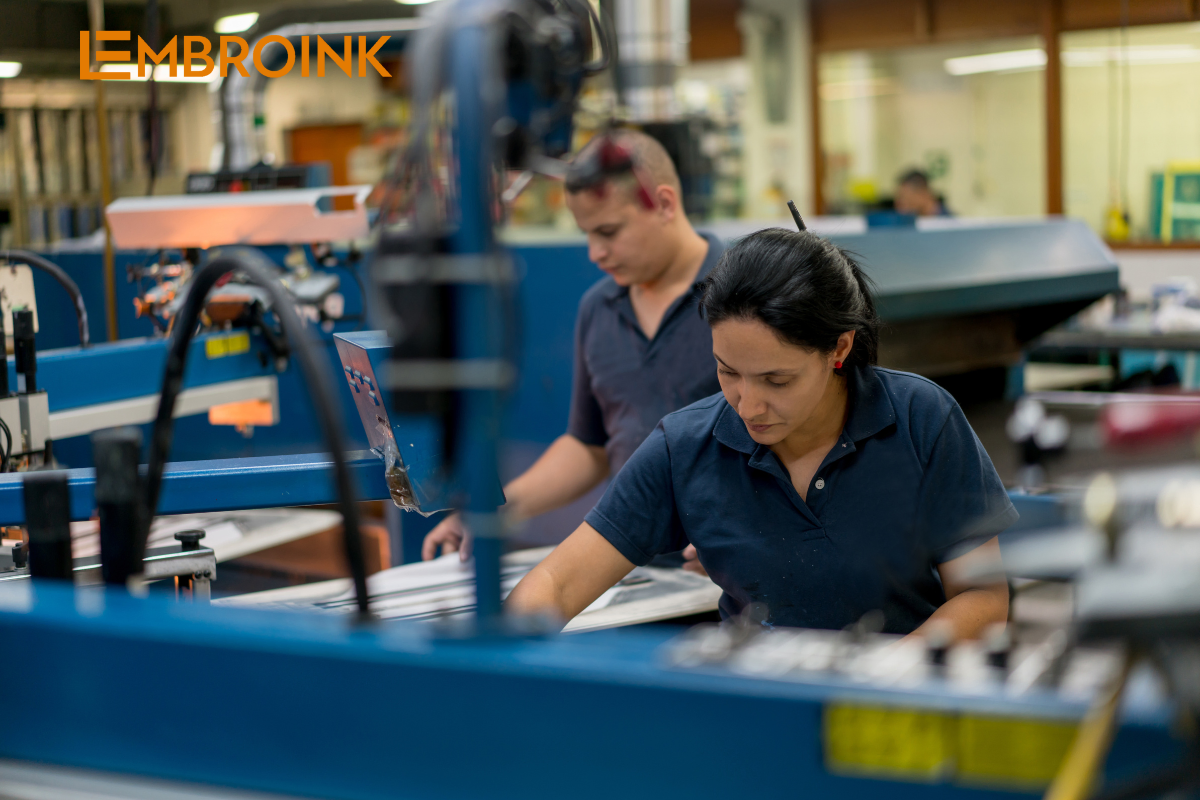
Direct-to-Film vs. Sublimation Printing
Sublimation printing:
Sublimation printing involves printing designs onto special sublimation paper and then transferring them to fabric using a heat press. This process allows for full-coverage, vibrant prints that become part of the fabric. However, sublimation can be time-consuming due to the preparation and transfer steps involved. It is primarily suited for polyester and polymer-coated fabrics, and is also used for various products such as mouse pads, mugs, and blankets. This technique is best for items where full-color, all-over prints are desired on polyester or polyester blends.
Direct-to-Film (DTF) printing:
- Process: Designs are printed onto PET film, with an adhesive powder applied, then heat-transferred to fabric. This method allows for detailed and vibrant prints.
- Time: Generally faster than sublimation, as it skips the paper transfer step and directly applies the design to the fabric.
- Fabric compatibility: Works with a wide range of fabrics, including polyester, cotton, fleece, and nylon. Unlike sublimation, it does not require polyester blends.
- Best suited for: Versatile applications, including various fabric types and detailed designs.
If your product range includes a variety of fabric types beyond polyester, DTF printing offers greater flexibility. Sublimation remains a strong choice for full-coverage prints on polyester fabrics and related items.
Explore more about printing techniques in our other posts comparing sublimation and screen printing, as well as DTG and screen printing, to find the best fit for your business.
Direct-to-Film Printing at printful
At Printful, we’re committed to delivering the best experience for our print-on-demand customers. Currently, we offer Direct-to-Film (DTF) printing for a select range of products. As we continue to refine the process, we’re excited about the prospect of expanding our product lineup to include more items using this technique. We are dedicated to perfecting DTF printing and look forward to broadening our offerings once we’ve fully mastered this method.
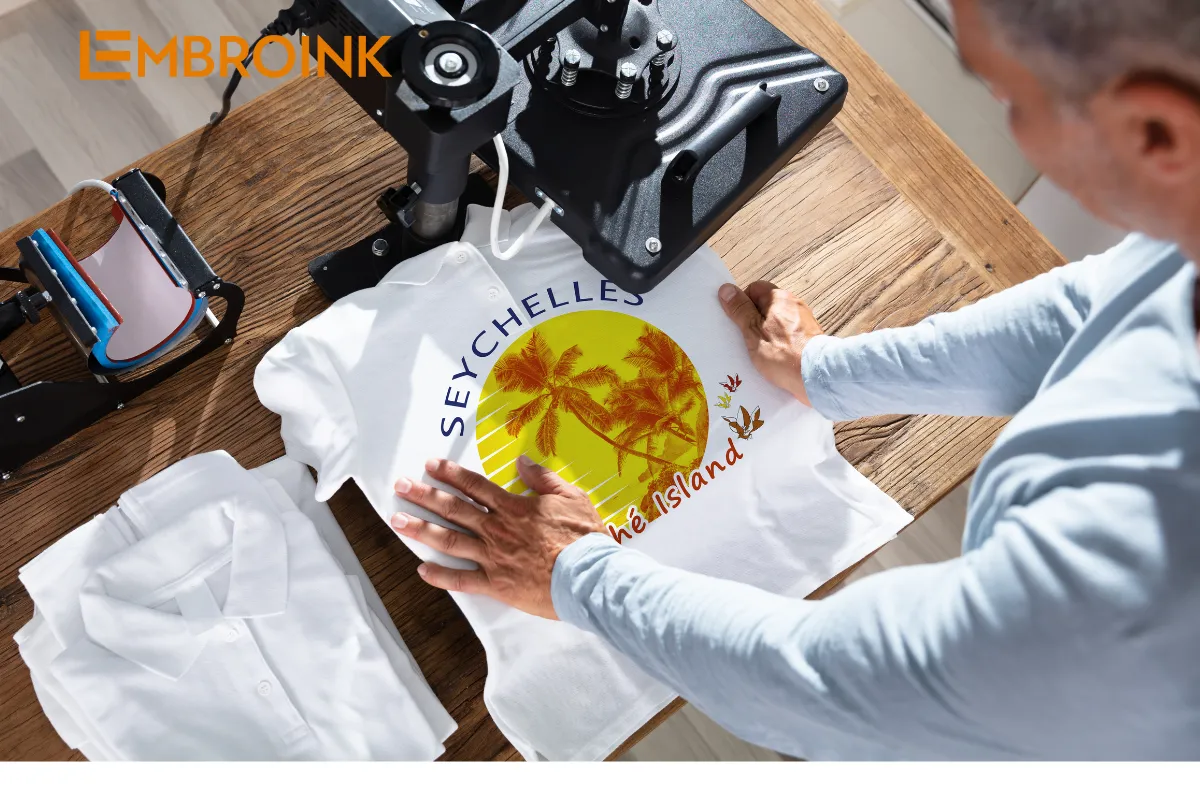
How to prepare a print file for Direct-to-Film printing
To ensure high-quality results with Direct-to-Film (DTF) printing, follow these guidelines:
File type and graphics resolution:
- File type: Use a PDF file with a transparent background for best results.
- Resolution: A resolution of at least 300 DPI is recommended to achieve a sharp, crisp final design.
Semi-Transparencies:
- Avoid Semi-Transparencies: These often result in poor print quality for DTF printing. Semi-transparent areas can cause visible edges and a dotted, fuzzy halftone effect in the final print.
Colors and Color Gamut:
- Color gamut: We use the CYMK PSO V3 color gamut. For more vibrant print performance, CMYK colors tend to be more saturated.
- Neon colors: Neon colors may appear differently in the final print because the printer will select the closest available color if it cannot match the neon shades exactly.
- Recommended color profile: Use the sRGB IEC61966-2.1 color profile. This profile is easier to manage compared to CYMK files, which are larger and require advanced graphics software. sRGB is widely used in the custom-printing industry and offers reliable results.
By following these guidelines, you can ensure your DTF prints look as vibrant and detailed as intended.
Now you know everything about Direct-to-Film printing
DTF printing is a versatile method that works well on a variety of fabrics, delivering vibrant and durable designs, especially for intricate details and diverse elements.
If you’re looking to expand your product offerings with a new printing technique, DTF printing is worth considering. Register to stay updated on when more products will become available for design using this innovative method.