When did computerized embroidery technology come into existence?
As life becomes increasingly modern and advanced, machines seem to have replaced humans in performing almost every task. This shift is evident in the textile industry as well. Instead of manually stitching each thread with a needle, machines can now accomplish this task at a faster pace, yielding higher-quality products. In this context, modern technology that EmbroInk wishes to highlight is computerized embroidery technology. So, what exactly is computerized embroidery? Let’s explore some useful information to understand more about this unique form of creativity.
What is computerized embroidery?
Computerized embroidery, or digital embroidery, is a method of stitching using machines that relies on the same principles as manual embroidery but without direct human hand manipulation. Instead, it operates through pre-programmed code lines within a computer. This technology allows for faster stitching speeds, reducing labor intensity and shortening production times.
Named for its reliance on state-of-the-art machinery, computerized embroidery ensures high precision and durability in the products it creates. Moreover, due to its intelligent operation, machines can embroider multiple different patterns simultaneously.
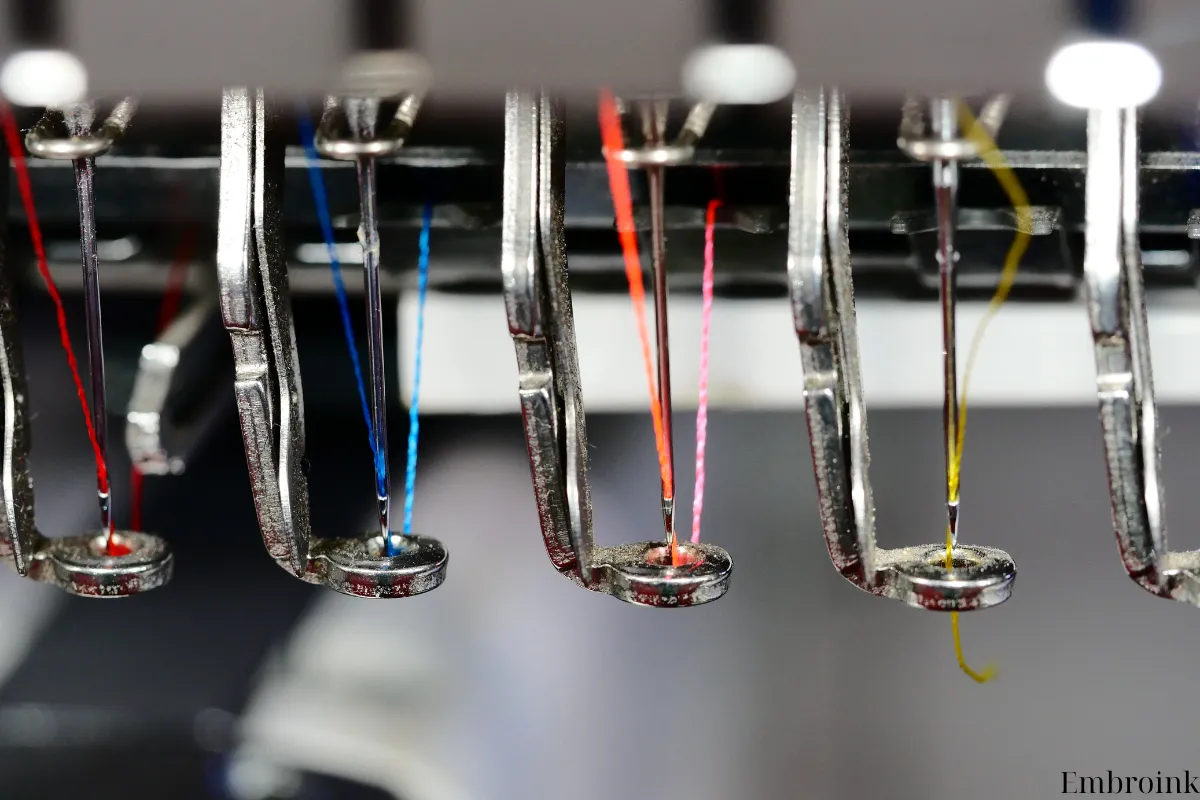
When did computerized embroidery technology come into existence?
Computerized embroidery technology emerged as a significant advancement in the fashion industry. The initial conceptualization can be traced back to Peter Haase, a Dutch scientist, who developed a prototype involving punching designs through paper tape and feeding them into an embroidery machine. However, this early method was prone to failure with minor errors.
The first practical embroidery machine, the Tajima, was invented in the mid-1960s, laying the groundwork for further innovations. Peter Haase later refined this concept, but technical limitations prevented its widespread adoption.
In the 1980s, computerized embroidery systems began to be utilized more widely, initially on mini computers, thanks to Wilcom’s introduction of embroidery software. The international distribution network Melco also played a pivotal role by developing the first embroidery sample head for use with large Schiffli frames, founded by Randal Melton and Bill Childs.
By 1984, automated embroidery machines were developed, leveraging CAD embroidery design software and CAM controllers. In Vietnam, automated embroidery technology was introduced around 1990, primarily relying on customer-provided embroidery designs at that time.
The advent of computerized embroidery marked a significant leap forward in the fashion industry, offering numerous advantages in terms of time efficiency, cost-effectiveness, production volume, and quality. These advancements have effectively met market demands and consumer preferences, shaping the modern landscape of textile production.
Advantage and disadvantages of computerized embroidery
Advantage
Computerized embroidery offers several significant advantages over traditional hand embroidery:
- High Precision: Computerized embroidery ensures precise stitching as each needle and thread path is predefined in the program. This results in consistent and accurate reproduction of the design with preset speeds and sizes. Monitoring the embroidery process ensures that the output matches the uploaded design.
- Fast Speed: Unlike hand embroidery, which is labor-intensive and time-consuming, computerized embroidery operates at much faster speeds. This increases production efficiency, reduces labor costs, and enables quicker completion of designs. Some designs can be finished within minutes using computerized embroidery technology.
- Cost Efficiency: By reducing labor costs and increasing production output, computerized embroidery significantly lowers overall production costs. The efficiency gains translate into higher profit margins due to increased productivity per unit of time.
- Flexibility: Computerized embroidery is versatile and can be applied to a wide range of textile products. Whether it’s clothing, accessories, or other items, the technology can handle various types of embroidery tasks effectively.
Overall, these advantages make computerized embroidery a preferred choice for modern textile production, offering efficiency, precision, and cost-effectiveness that traditional methods cannot match.
Disadvantages
Here is the translation of the disadvantages of computerized embroidery technology:
- High Costs: Setting up computerized embroidery systems requires a significant initial investment. Businesses need to allocate a large budget for purchasing machinery, software, and system installation. This is one of the major drawbacks of this technology.
- Complexity in Usage: Managing and operating computerized embroidery systems requires personnel with deep technical knowledge of computers and programming. Delegating tasks to untrained individuals can result in inaccurate embroidery or failure to meet requirements.
- Limited Human Intervention: Computerized embroidery machines often come with automated tension control systems to adjust thread tension based on fabric type and design pattern. However, this also means operators cannot manually intervene to make adjustments as needed.
- High Repair Costs: Due to their fully automated nature, repairing computerized embroidery machines can be costly and complex when malfunctions occur. Moreover, finding skilled repair professionals to troubleshoot these issues can be challenging.
These drawbacks should be carefully considered by businesses when deciding to invest in computerized embroidery technology, in order to fully leverage its benefits.
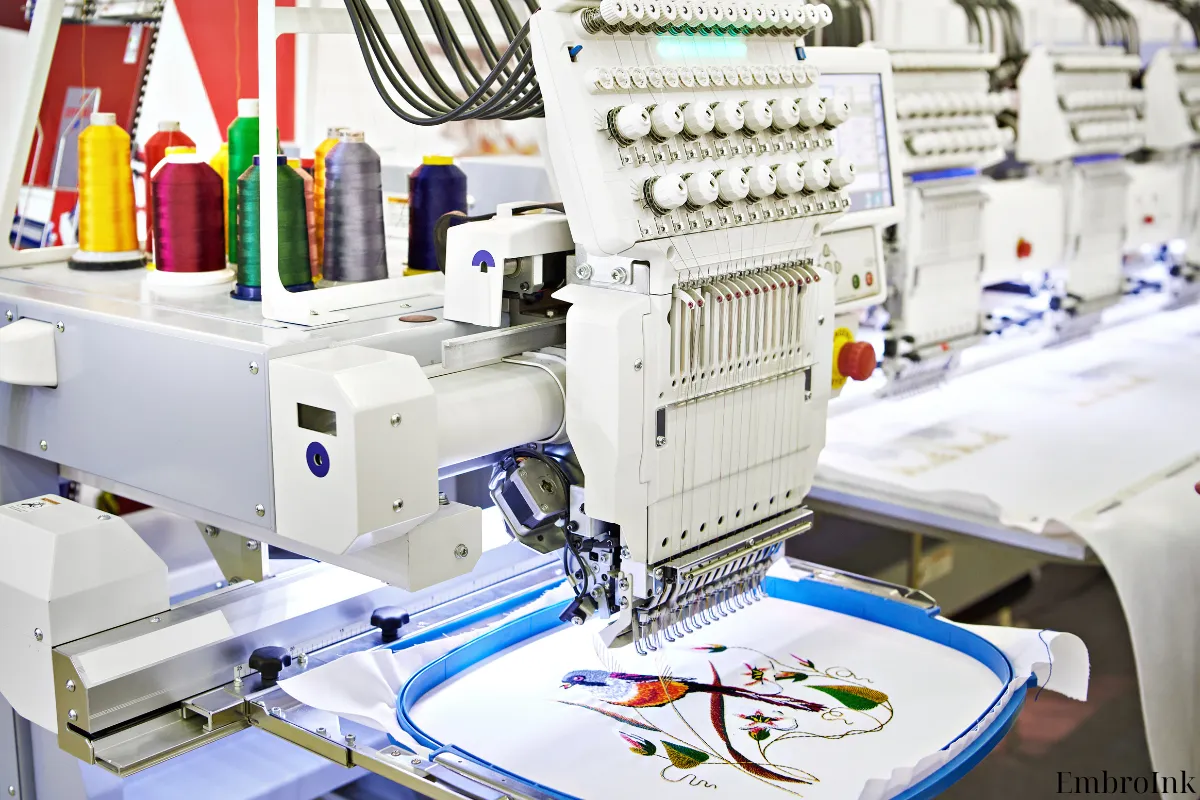
Features of computerized embroidery
Modern Technology:
- Machine embroidery: Computerized embroidery utilizes specialized machinery with advanced technology, programmed to automatically execute embroidery stitches according to digitized designs.
- Advancements in technology: The advancements in technology enable embroidery machines to operate with high precision and efficiency, resulting in products with consistent and stable quality.
- Capability for complex designs: Modern embroidery machines can execute complex embroidery patterns with exquisite precision and detail.
Digitization of design process:
- Before execution, designs are converted from manual to digital format through specialized software.
- The digitization process allows for easy editing and adjustment of designs according to customer requirements.
- The digitized data is then loaded into the embroidery machine, enabling it to execute stitches according to the programmed design.
Mass production capability:
- Computerized embroidery has the capability for mass production in large quantities within a short time frame while ensuring the quality and accuracy of the products.
- This is suitable for large orders such as corporate uniforms, team uniforms, or advertising products with large quantity requirements and quick turnaround times.
This section analyzes the basic characteristics of Computerized embroidery, from the technology used to the production process and mass production capability. This helps to understand the convenience and efficiency of this embroidery method in custom embroidery services.
Production and shipping time of Embroink
After completing and adjusting the embroidered product according to the requirements, the next step is to finalize and deliver the product to the customer. This process involves important steps such as trimming and cleaning the product to remove any excess thread, making the product neater and sharper. Additionally, re-inspecting the product before packaging is crucial to ensure that no defects are present and that every detail meets the highest quality standards.
Next, the embroidered product will be carefully and securely packaged to protect it during transportation and storage. Choosing appropriate packaging materials such as plastic bags, cardboard boxes, or fabric pouches also plays a crucial role in ensuring that the product remains intact during transportation.
Finally, the embroidered product will be delivered to the customer according to the agreed-upon location and delivery time. This needs to be done safely and punctually, accompanied by providing usage and care instructions if necessary. The process of finalizing and delivering the product not only marks the end of the production process but also provides an opportunity to make a positive impression and enhance the relationship with the customer.
Our goal is to process your orders promptly and efficiently:
- Production Time: 1 to 2 business days depending on the product and order complexity.
- Tracking Information: Tracking numbers are provided within 2 days of receiving payment for that orders. Tracking becomes active once the shipment reaches the destination country.
Estimated Shipping Time:
- US: Approximately 3 to 9 business days.
- UK & EU: Approximately 10 to 14 business days.
- *Orders to the EU that want to include tax will add $7 (orders need to have the consignee’s phone number and email)
- Other Countries: Approximately 21 to 30 business days.
Please note that delays may occur due to factors beyond our control such as customs delays or logistical issues. In such cases, while we will assist in resolving the issue with the carrier, we cannot guarantee immediate resolution.
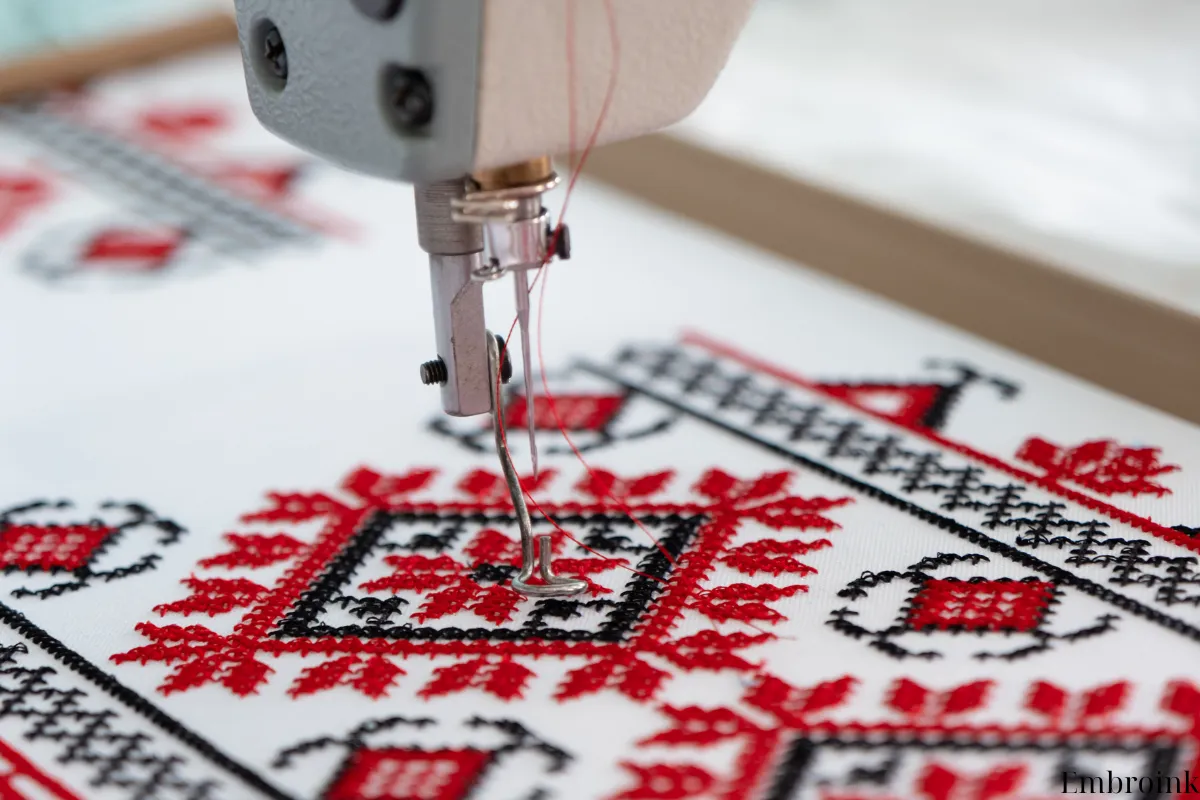
Commitments of Embroink
Embroink is dedicated to providing the highest level of service, but there are certain situations where we cannot be held liable:
- We do not assume responsibility for orders if customers directly modify addresses with carriers.
- We are not responsible for inaccuracies in shipping addresses provided by the buyer.
- Customs fees or taxes are not covered by us; sellers are responsible for informing their customers about potential duties.
- If a customer refuses to pay customs duties and the order is returned, we do not refund these costs.
- We cannot address issues with orders claimed as undelivered if tracking information confirms delivery. (However, we are willing to collaborate with the shipping company to request maximum evidence)
Regarding Product Issues and Resolutions:
- To efficiently address product-related concerns, we require:
- A photo of the shipping label.
- Clear images of defects for items such as incorrect sizes, colors, or defective merchandise.
- Complaints must be lodged within 30 days of product delivery.
- For embroidery products, please be aware that ink marks from the design process are normal and will wash out. We consider this as non-defective.
- If a product is determined to be defective, and the fault lies with us, we will either resend the product at no extra cost or provide a refund of the base cost.