A comprehensive guide to Direct to Film – DTF Printing
When it comes to printing, understanding your options is essential. Amid the myriad choices available, Direct-to-Film (DTF) printing stands out as a versatile and innovative method. Imagine it as a gateway to limitless design possibilities and vibrant color options for your products. But what exactly is DTF printing? How does it simplify the intricate world of digital printing?
This guide of EmbroInk will explore the fundamentals of DTF printing, equipping you with the knowledge to navigate and leverage this exciting technology for your product customization needs.
What is Direct-to-Film (DTF) transfer?
Direct-to-Film (DTF) transfer is a cutting-edge printing technique used primarily in garment decoration. It employs advanced inkjet technology to print detailed designs onto a special film. This film is then transferred to the garment using a heat press, where the ink adheres directly to the fabric fibers. The result is a high-quality, durable print that can capture intricate details and vibrant colors.
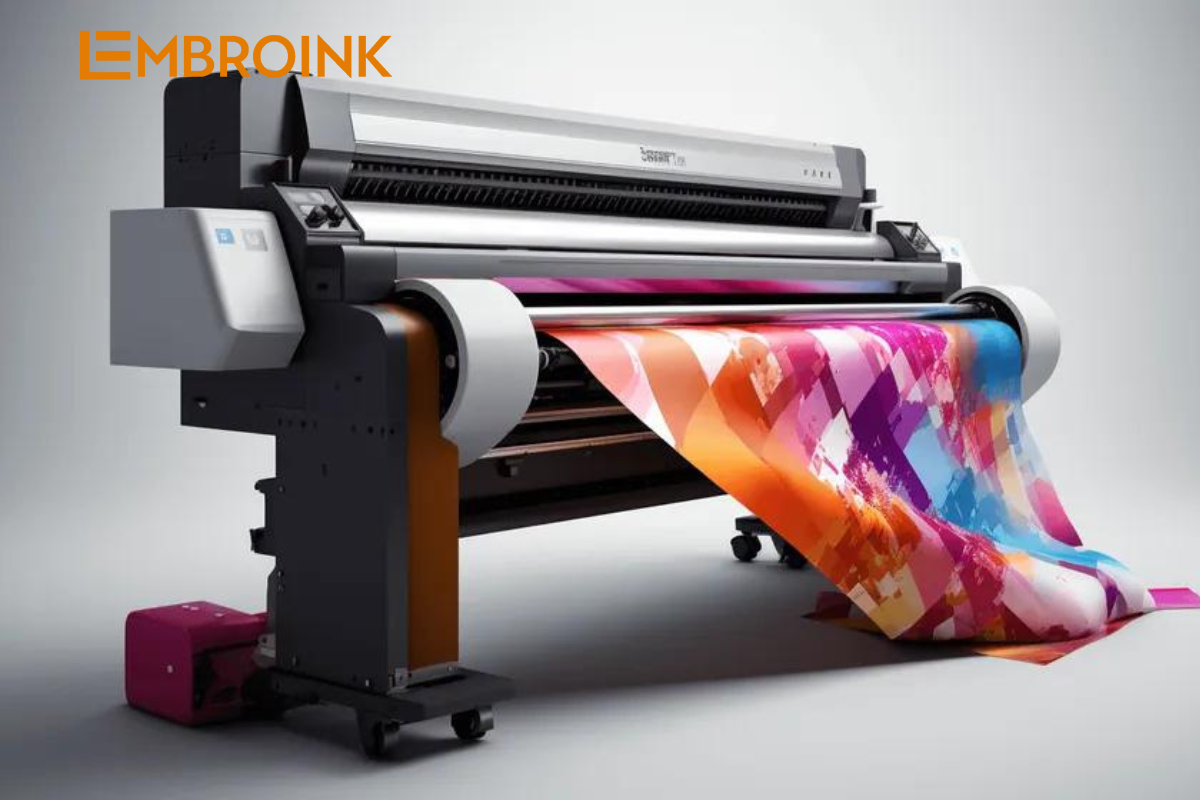
Essential components for DTF Printing
To successfully carry out a DTF printing project, you’ll need several key components. Here are the five essentials:
- DTF Printer: A specialized or modified inkjet printer tailored for film printing. Epson-based printers with piezoelectric printheads are commonly used in DTF applications.
- Specialized DTF inks: These inks are designed to adhere to the film and come in two types: CMYK process colors and white under-base ink.
- DTF Films: Non-adhesive films used to print the design. The film holds the ink and adhesive powder, and it dissolves under heat, leaving the print on the substrate.
- Powder adhesive: A powder that is sprinkled onto the film after printing. When heated, it melts and creates a strong bond between the print and the transfer material.
- Heat press: A machine used to transfer the design from the film to the material. The heat press melts the film and adhesive, ensuring the design is firmly attached to the substrate.
An Overview of the DTF Printing Process
Here’s a step-by-step guide to the DTF printing process:
- Design creation: Develop or modify your digital design using graphic design software like Photoshop.
- Conversion to printable format: Finalize your design and convert it into a format compatible with DTF printing.
- Printing on release film: Use a DTF printer to print the design onto a special release film. DTF printers utilize CMYK (Cyan, Magenta, Yellow, and Black) plus White inks to achieve vibrant prints.
- Applying adhesive powder: While printing, apply a unique adhesive powder to the wet ink on the film. This powder ensures that the design adheres properly to the final substrate, such as t-shirts or bags.
- Drying and melting adhesive: Pass the film through a ‘powder shaking machine’ to dry and evenly distribute the adhesive powder. This process helps in melting and setting the adhesive.
- Transferring to the final product: Position the film on the final product and use a heat press machine to transfer the design. The heat press applies specific temperature and pressure to bond the design to the fabric.
- Revealing the design: Once the product has cooled, peel away the release film to reveal the vibrant, durable design.
The result is a high-quality product with a beautifully transferred design, ready for display or sale.
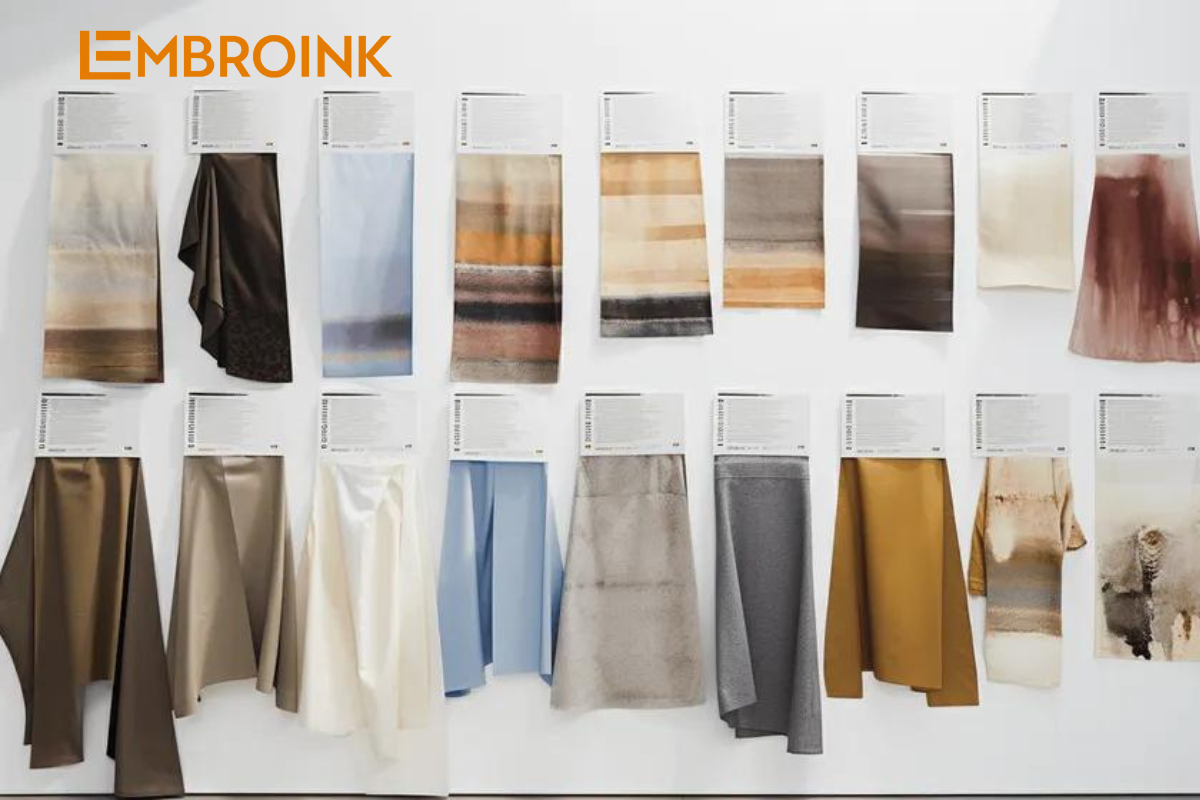
Advantages of DTF Printing
DTF printing revolutionizes the print industry with its many benefits, making it a compelling choice for creators and artists. Here’s a look at its main advantages:
Versatility
DTF printing excels in adaptability, allowing you to print on a wide range of fabrics and materials. It handles complex designs with multiple colors, gradients, and shading with precision. Beyond garments, it can be used on hats, bags, shoes, and even pillows. This flexibility provides a vast playground for artists and creators to explore unique materials and custom wearable art.
Full-Color printing
One of DTF’s standout features is its ability to reproduce vibrant, full-color designs without limiting your color palette. Whether your design includes subtle hues or bold, bright tones, DTF printing can render intricate details and colors accurately, preserving the quality of high-resolution images on fabric.
Durability
DTF prints are known for their longevity and resistance to wear and tear. They maintain their vibrant colors and detailed designs even after multiple washes. This durability ensures that printed items look as fresh as the day they were made, making DTF a preferred choice for creators and businesses focused on high-quality, long-lasting products.
Cost-Effectiveness
DTF printing offers a cost-effective solution, particularly for bulk orders. The process is affordable, with minimal equipment investment required. Additionally, DTF reduces labor costs due to its straightforward process and generates less waste compared to other methods, further lowering operational costs.
Fabric compatibility
This method is highly adaptable to various fabric types, including cotton, polyester, and blends. Whether working with sturdy materials like denim or delicate fabrics like silk, DTF printing delivers consistent, high-quality results. This adaptability is ideal for creators looking to experiment with different substrates and push the boundaries of apparel and merchandise customization.
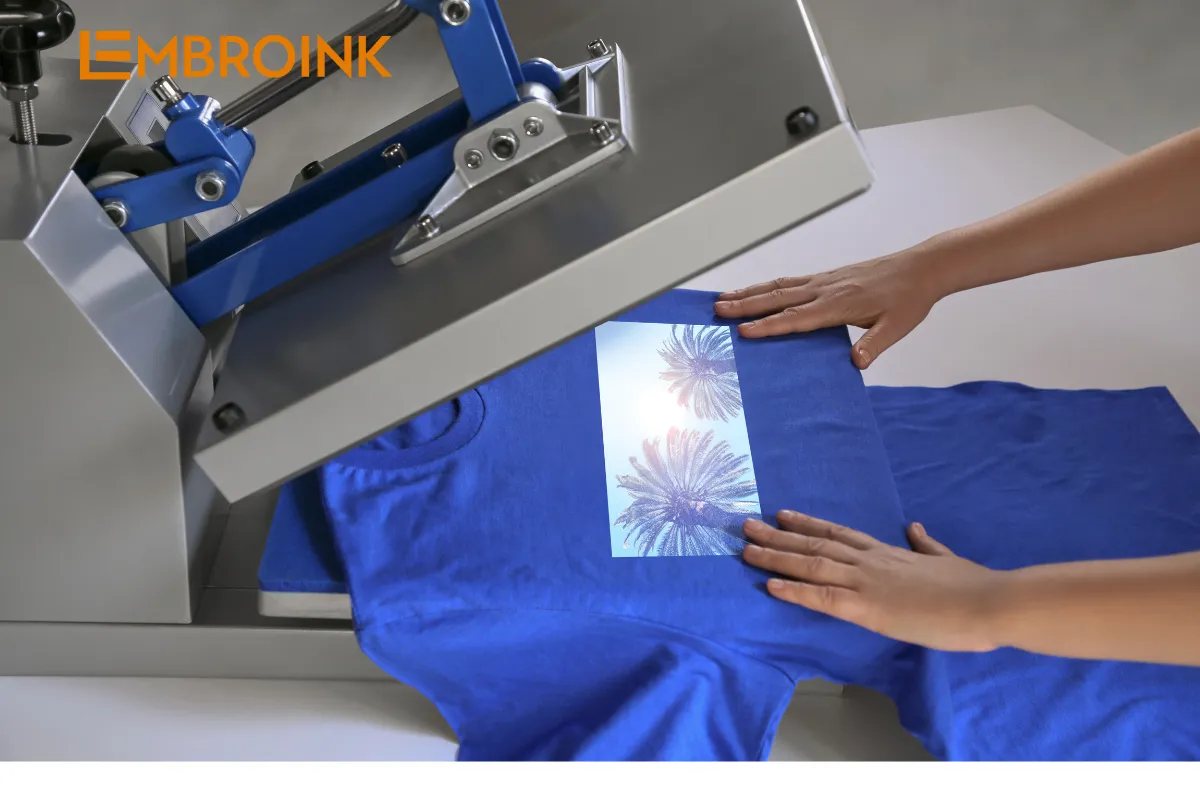
Limitations of DTF Printing
Despite its advantages, DTF printing comes with some limitations and challenges. Here are the primary drawbacks to consider:
Lengthy production time
DTF printing can be quite time-consuming due to its multi-stage process. From designing and printing on the film to curing the design onto the material, each step adds time to the overall production. For businesses needing quick turnaround times or managing large volumes, this extended timeline can lead to delays and potentially impact customer satisfaction.
Difficult to scale
Scaling up DTF production can be complex due to the intricate nature of the process. Increasing production volumes requires more storage space and additional manpower. Additionally, the need for specialized heat press machines and the potential for inconsistent quality in bulk orders can pose significant challenges to scaling.
Environmental impact
DTF printing has environmental concerns, particularly due to the use of acetate film and petrochemical inks, which are non-biodegradable and contribute to plastic waste. The process also involves substantial electricity consumption and heat waste from curing units. Furthermore, proper disposal of leftover inks and solvents is crucial to avoid water and soil pollution.
Poor print breathability and feel
The adhesive powder used in DTF printing can affect the fabric’s breathability. The final print may feel rubbery or stiff, which can reduce comfort, especially in warmer conditions. This can make the garment less pleasant to wear compared to other printing methods that offer a softer touch and better airflow.
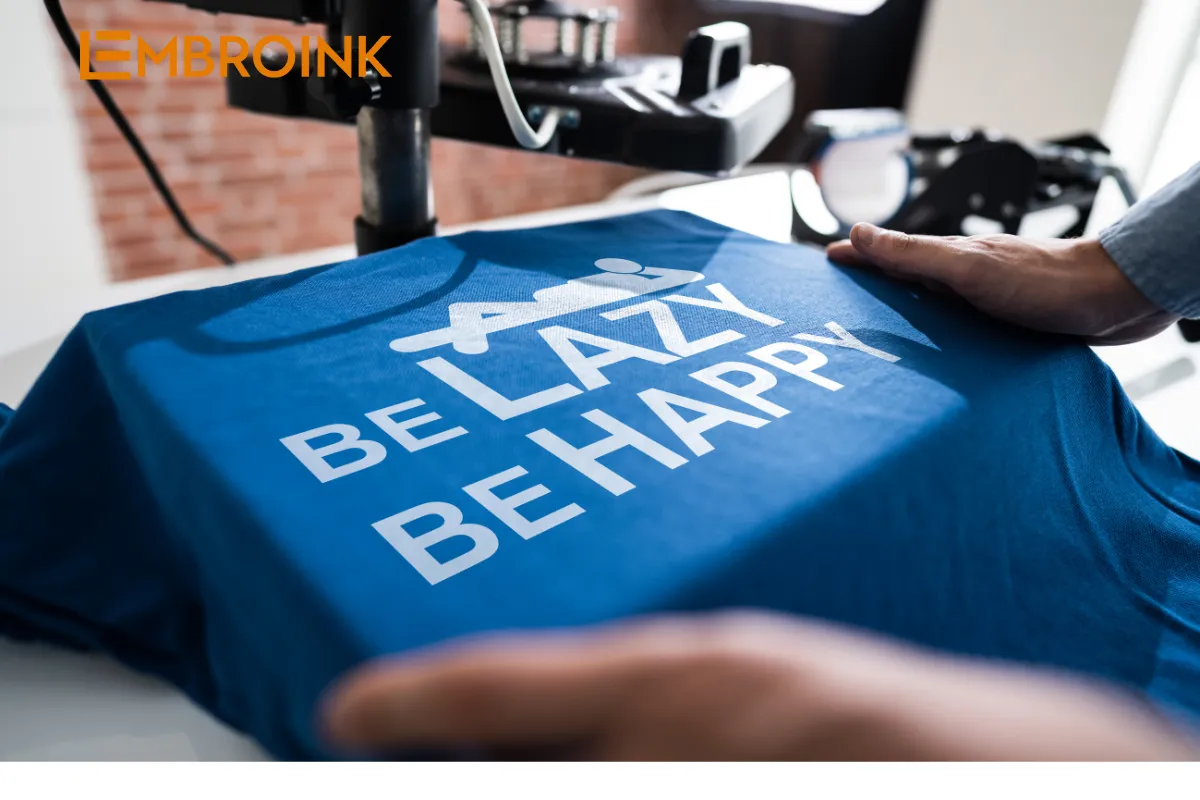
Comparing DTF with other printing methods
Understanding the differences between DTF printing and other popular methods can help you choose the best technique for your projects. Here’s a comparison of DTF printing with several other methods:
DTF Printing vs. DTG Printing
-
- DTF Printing: Direct-to-Film (DTF) printing transfers designs onto a wide range of materials using heat. It excels at creating vivid, full-color prints, even on darker fabrics. However, DTF prints can sometimes feel stiff or heavy, and their durability may diminish after multiple washes.
- DTG Printing: Direct-to-Garment (DTG) printing sprays ink directly onto the fabric, producing designs with a soft and natural feel. It offers high-resolution, detailed prints and retains vibrancy even after many washes. DTG is ideal for intricate designs with multiple colors, but it’s generally limited to cotton and similar fabrics.
DTF Printing vs. Screen Printing
-
- DTF Printing: Utilizes modern technology to transfer complex, multi-colored designs with high precision directly onto fabrics. It’s versatile and effective for various materials but may be less efficient for very large production runs.
- Screen Printing: Involves creating a stencil (screen) and applying ink through it, making it well-suited for large batches of the same design. While it’s cost-effective for high volumes, the setup can be labor-intensive and complex, especially for designs with multiple colors.
DTF Printing vs. Sublimation Printing
-
- Sublimation Printing: Uses heat to turn ink into gas, which then permeates the fabric, resulting in vibrant, high-definition designs that are integrated into the material. Best for polyester fabrics or coated hard substrates, sublimation is efficient for bulk production and offers excellent durability.
- DTF Printing: Prints designs onto a film, which is then transferred onto a wider range of fabrics, including cotton, nylon, and leather. DTF prints have a more noticeable texture compared to sublimation prints but are highly detailed and colorful.
DTF Printing vs. Heat transfer Printing
-
- Heat Transfer Printing: Involves printing designs onto heat transfer paper, which is then transferred onto the fabric using a heat press. This method can be more costly due to the need for specialty paper and can result in variable quality based on paper and application techniques.
- DTF Printing: Offers a full-color spectrum with smoother results and better durability compared to heat transfer printing. DTF’s versatility in fabric compatibility and overall quality often surpasses heat transfer methods, making it a preferred choice for many applications.
Each printing method has its strengths and weaknesses, and the choice between them will depend on factors such as fabric type, design complexity, production volume, and budget.
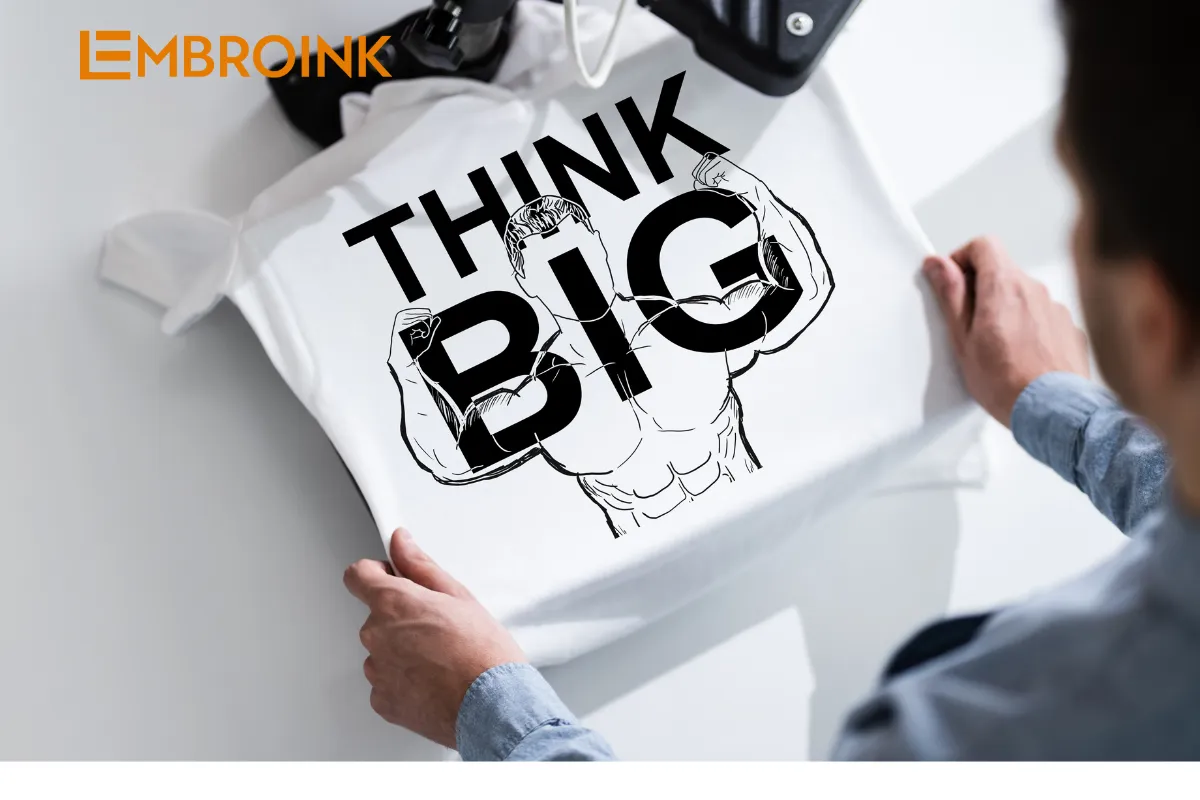
How to choose the right printing method
Selecting the right printing method can be challenging with so many options available. To help you make an informed decision, consider these five essential tips:
- Understand your needs: Assess the specific requirements of your project. Are you working with dark fabrics or need intricate, detailed designs? Determine the finish, texture, and durability you want. For example, if you need vibrant colors and complex details, methods like DTG or DTF might be ideal. For a vintage look or more subtle designs, other techniques might be better suited.
- Know budget: Different printing methods come with varying costs. DTG and DTF might have lower setup costs but can be pricier per item. In contrast, screen printing becomes more economical with larger print runs due to lower per-unit costs. Evaluate your budget and production volume to find the most cost-effective solution for your needs.
- Evaluate print quality: The quality of prints varies by method. DTG and DTF are known for their high-resolution capabilities and detailed results. If you require sharp, intricate designs, these methods may be preferable. For simpler designs, other methods like screen printing might be sufficient and more cost-effective.
- Consider the fabric: Different fabrics react differently to printing methods. DTF is versatile and works on various materials, but it may not offer the same soft feel as DTG, especially on certain fabrics. Evaluate how each method affects the feel and look of the fabric you’re using to ensure it meets your expectations.
- Environmental impact: With growing environmental awareness, it’s important to consider the ecological footprint of your chosen printing method. Some methods, like dye sublimation or heat transfer, can have a larger environmental impact due to chemical use and waste. DTG and DTF may have lesser environmental concerns, but it’s still worth assessing the overall sustainability of each method.
By carefully considering these factors, you can choose the printing method that best aligns with your project’s requirements, budget, and environmental considerations.